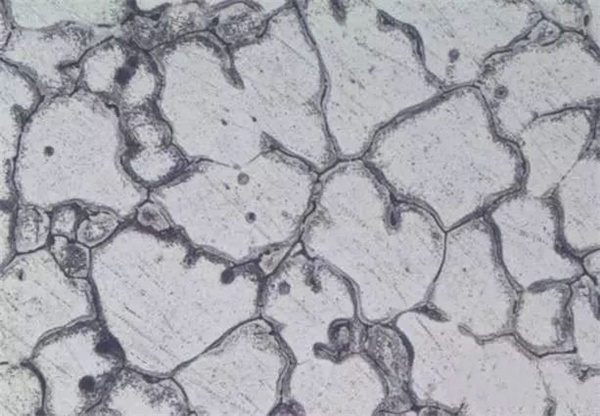
I. ਛੋਟਾ ਕਰਨਾ
ਕੁਝ ਐਕਸਟਰੂਡ ਉਤਪਾਦਾਂ ਦੇ ਪੂਛ ਦੇ ਸਿਰੇ 'ਤੇ, ਘੱਟ ਵੱਡਦਰਸ਼ੀ ਨਿਰੀਖਣ ਤੋਂ ਬਾਅਦ, ਕਰਾਸ ਸੈਕਸ਼ਨ ਦੇ ਵਿਚਕਾਰਲੇ ਹਿੱਸੇ ਵਿੱਚ ਇੱਕ ਸਿੰਗ ਵਰਗੀ ਘਟਨਾ ਹੁੰਦੀ ਹੈ, ਜਿਸ ਨੂੰ ਸੁੰਗੜਦੀ ਪੂਛ ਕਿਹਾ ਜਾਂਦਾ ਹੈ।
ਆਮ ਤੌਰ 'ਤੇ, ਫਾਰਵਰਡ ਐਕਸਟਰੂਜ਼ਨ ਉਤਪਾਦ ਦੀ ਪੂਛ ਰਿਵਰਸ ਐਕਸਟਰਿਊਜ਼ਨ ਨਾਲੋਂ ਲੰਬੀ ਹੁੰਦੀ ਹੈ, ਅਤੇ ਨਰਮ ਮਿਸ਼ਰਤ ਕਠੋਰ ਮਿਸ਼ਰਤ ਨਾਲੋਂ ਲੰਬੀ ਹੁੰਦੀ ਹੈ।ਅੱਗੇ ਬਾਹਰ ਕੱਢੇ ਉਤਪਾਦ ਦਾ ਸੁੰਗੜਨਾ ਜਿਆਦਾਤਰ ਇੱਕ ਐਨੁਲਰ ਡਿਸਜੋਇੰਟ ਪਰਤ ਦੇ ਰੂਪ ਵਿੱਚ ਹੁੰਦਾ ਹੈ, ਅਤੇ ਰਿਵਰਸ ਐਕਸਟਰੂਡ ਉਤਪਾਦ ਦਾ ਸੁੰਗੜਨਾ ਜਿਆਦਾਤਰ ਇੱਕ ਕੇਂਦਰੀ ਫਨਲ ਦੀ ਸ਼ਕਲ ਵਿੱਚ ਹੁੰਦਾ ਹੈ।
ਧਾਤ ਨੂੰ ਪਿਛਲੇ ਸਿਰੇ ਤੱਕ ਬਾਹਰ ਕੱਢਿਆ ਜਾਂਦਾ ਹੈ, ਅਤੇ ਇੱਕ ਸੈਕੰਡਰੀ ਸੰਕੁਚਨ ਬਣਾਉਣ ਲਈ ਐਕਸਟਰੂਜ਼ਨ ਸਿਲੰਡਰ ਦੇ ਮਰੇ ਕੋਨੇ ਜਾਂ ਗੈਸਕੇਟ ਦੇ ਵਹਾਅ 'ਤੇ ਇਕੱਠੀ ਹੋਈ ਪਿੰਜੀ ਦੀ ਚਮੜੀ ਅਤੇ ਵਿਦੇਸ਼ੀ ਸੰਮਿਲਨ;ਜਦੋਂ ਬਚੀ ਹੋਈ ਸਮੱਗਰੀ ਬਹੁਤ ਛੋਟੀ ਹੁੰਦੀ ਹੈ ਅਤੇ ਉਤਪਾਦ ਦਾ ਕੇਂਦਰ ਨਾਕਾਫ਼ੀ ਤੌਰ 'ਤੇ ਖੁਆਇਆ ਜਾਂਦਾ ਹੈ, ਤਾਂ ਇਹ ਇੱਕ ਕਿਸਮ ਦਾ ਸੰਖੇਪ ਰੂਪ ਬਣਦਾ ਹੈ।ਪੂਛ ਦੇ ਸਿਰੇ ਤੋਂ ਅੱਗੇ ਤੱਕ, ਪੂਛ ਹੌਲੀ-ਹੌਲੀ ਹਲਕਾ ਹੋ ਜਾਂਦੀ ਹੈ ਅਤੇ ਪੂਰੀ ਤਰ੍ਹਾਂ ਅਲੋਪ ਹੋ ਜਾਂਦੀ ਹੈ।
ਸੁੰਗੜਨ ਦਾ ਮੁੱਖ ਕਾਰਨ
1. ਬਚੀ ਹੋਈ ਸਮੱਗਰੀ ਬਹੁਤ ਛੋਟੀ ਹੈ ਜਾਂ ਉਤਪਾਦ ਦੇ ਕੱਟੇ ਸਿਰੇ ਦੀ ਲੰਬਾਈ ਨਿਯਮਾਂ ਨੂੰ ਪੂਰਾ ਨਹੀਂ ਕਰਦੀ ਹੈ;
2. ਐਕਸਟਰਿਊਸ਼ਨ ਪੈਡ ਸਾਫ਼ ਨਹੀਂ ਹੈ ਅਤੇ ਤੇਲ ਦੇ ਧੱਬੇ ਹਨ;
3. ਬਾਹਰ ਕੱਢਣ ਦੇ ਬਾਅਦ ਦੇ ਪੜਾਅ ਵਿੱਚ, ਬਾਹਰ ਕੱਢਣ ਦੀ ਗਤੀ ਬਹੁਤ ਤੇਜ਼ ਹੈ ਜਾਂ ਅਚਾਨਕ ਵਧ ਜਾਂਦੀ ਹੈ;
4. ਇੱਕ ਵਿਗੜਿਆ ਸਕਿਊਜ਼ ਪੈਡ (ਵਿਚਕਾਰ ਵਿੱਚ ਇੱਕ ਉੱਚਾ ਪੈਡ) ਦੀ ਵਰਤੋਂ ਕਰੋ;
5. ਐਕਸਟਰਿਊਸ਼ਨ ਸਿਲੰਡਰ ਦਾ ਤਾਪਮਾਨ ਬਹੁਤ ਜ਼ਿਆਦਾ ਹੈ;
6. ਐਕਸਟਰੂਜ਼ਨ ਸਿਲੰਡਰ ਅਤੇ ਐਕਸਟਰੂਜ਼ਨ ਸ਼ਾਫਟ ਇਕਸਾਰ ਨਹੀਂ ਹਨ;
7. ਪਿੰਜੀ ਦੀ ਸਤ੍ਹਾ ਸਾਫ਼ ਨਹੀਂ ਹੈ, ਤੇਲ ਦੇ ਧੱਬੇ ਹਨ, ਵੱਖ ਕਰਨ ਵਾਲੀਆਂ ਟਿਊਮਰ ਅਤੇ ਫੋਲਡਿੰਗ ਅਤੇ ਹੋਰ ਨੁਕਸ ਦੂਰ ਨਹੀਂ ਕੀਤੇ ਗਏ ਹਨ;
8. ਐਕਸਟਰਿਊਸ਼ਨ ਸਿਲੰਡਰ ਦੀ ਅੰਦਰਲੀ ਸਲੀਵ ਸਾਫ਼ ਜਾਂ ਖਰਾਬ ਨਹੀਂ ਹੈ, ਅਤੇ ਅੰਦਰਲੀ ਲਾਈਨਿੰਗ ਨੂੰ ਸਮੇਂ ਸਿਰ ਸਫਾਈ ਪੈਡ ਨਾਲ ਸਾਫ਼ ਨਹੀਂ ਕੀਤਾ ਜਾਂਦਾ ਹੈ।
ਰੋਕਥਾਮ ਵਿਧੀ
1. ਰਹਿੰਦ-ਖੂੰਹਦ ਛੱਡੋ ਅਤੇ ਲੋੜ ਅਨੁਸਾਰ ਪੂਛਾਂ ਨੂੰ ਕੱਟੋ;
2. ਮੋਲਡਾਂ ਨੂੰ ਸਾਫ਼ ਰੱਖੋ;
3. ਪਿੰਜਰੇ ਦੀ ਸਤਹ ਦੀ ਗੁਣਵੱਤਾ ਵਿੱਚ ਸੁਧਾਰ;
4. ਨਿਰਵਿਘਨ ਐਕਸਟਰਿਊਸ਼ਨ ਨੂੰ ਯਕੀਨੀ ਬਣਾਉਣ ਲਈ ਐਕਸਟਰਿਊਸ਼ਨ ਤਾਪਮਾਨ ਅਤੇ ਗਤੀ ਨੂੰ ਉਚਿਤ ਤੌਰ 'ਤੇ ਕੰਟਰੋਲ ਕਰੋ;
5. ਵਿਸ਼ੇਸ਼ ਹਾਲਾਤਾਂ ਨੂੰ ਛੱਡ ਕੇ, ਟੂਲ ਅਤੇ ਮੋਲਡ ਦੀ ਸਤਹ 'ਤੇ ਤੇਲ ਲਗਾਉਣ ਦੀ ਸਖ਼ਤ ਮਨਾਹੀ ਹੈ;
6. ਗੈਸਕੇਟ ਨੂੰ ਚੰਗੀ ਤਰ੍ਹਾਂ ਠੰਡਾ ਕੀਤਾ ਗਿਆ ਹੈ।
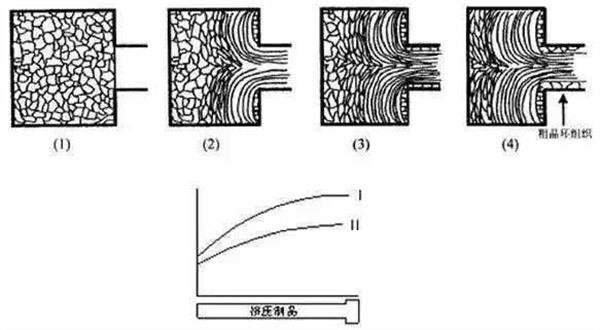
II.ਮੋਟੇ ਕ੍ਰਿਸਟਲ ਰਿੰਗ
ਕੁਝ ਅਲਮੀਨੀਅਮ ਮਿਸ਼ਰਤ ਐਕਸਟਰੂਡ ਉਤਪਾਦ ਘੋਲ ਦੇ ਇਲਾਜ ਤੋਂ ਬਾਅਦ ਘੱਟ ਵਿਸਤਾਰ ਟੈਸਟ ਦੇ ਟੁਕੜੇ 'ਤੇ ਉਤਪਾਦ ਦੇ ਘੇਰੇ ਦੇ ਨਾਲ ਇੱਕ ਮੋਟੇ ਰੀਕ੍ਰਿਸਟਾਲਾਈਜ਼ਡ ਅਨਾਜ ਬਣਤਰ ਖੇਤਰ ਬਣਾਉਂਦੇ ਹਨ, ਜਿਸ ਨੂੰ ਮੋਟੇ ਅਨਾਜ ਦੀ ਰਿੰਗ ਕਿਹਾ ਜਾਂਦਾ ਹੈ।ਉਤਪਾਦਾਂ ਦੇ ਵੱਖੋ-ਵੱਖਰੇ ਆਕਾਰਾਂ ਅਤੇ ਪ੍ਰਕਿਰਿਆ ਦੇ ਤਰੀਕਿਆਂ ਦੇ ਕਾਰਨ, ਰਿੰਗ-ਆਕਾਰ, ਚਾਪ-ਆਕਾਰ ਅਤੇ ਮੋਟੇ-ਦਾਣੇਦਾਰ ਰਿੰਗਾਂ ਦੇ ਹੋਰ ਰੂਪ ਬਣ ਸਕਦੇ ਹਨ।ਮੋਟੇ-ਦਾਣੇਦਾਰ ਰਿੰਗ ਦੀ ਡੂੰਘਾਈ ਹੌਲੀ-ਹੌਲੀ ਪੂਛ ਤੋਂ ਅੱਗੇ ਤੱਕ ਘਟਦੀ ਜਾਂਦੀ ਹੈ ਅਤੇ ਪੂਰੀ ਤਰ੍ਹਾਂ ਅਲੋਪ ਹੋ ਜਾਂਦੀ ਹੈ।ਪ੍ਰਾਇਮਰੀ ਗਠਨ ਵਿਧੀ ਉਪ-ਅਨਾਜ ਖੇਤਰ ਹੈ ਜੋ ਗਰਮ ਐਕਸਟਰਿਊਸ਼ਨ ਤੋਂ ਬਾਅਦ ਉਤਪਾਦ ਦੀ ਸਤ੍ਹਾ 'ਤੇ ਬਣਦਾ ਹੈ, ਅਤੇ ਮੋਟੇ ਰੀਕ੍ਰਿਸਟਾਲਾਈਜ਼ਡ ਅਨਾਜ ਖੇਤਰ ਨੂੰ ਗਰਮ ਕਰਨ ਅਤੇ ਘੋਲ ਦੇ ਇਲਾਜ ਤੋਂ ਬਾਅਦ ਬਣਾਇਆ ਜਾਂਦਾ ਹੈ।
ਮੋਟੇ ਕ੍ਰਿਸਟਲ ਰਿੰਗ ਦਾ ਮੁੱਖ ਕਾਰਨ
1. ਅਸਮਾਨ ਐਕਸਟਰਿਊਸ਼ਨ ਵਿਕਾਰ
2. ਗਰਮੀ ਦੇ ਇਲਾਜ ਦਾ ਤਾਪਮਾਨ ਬਹੁਤ ਜ਼ਿਆਦਾ ਹੈ ਅਤੇ ਹੋਲਡਿੰਗ ਸਮਾਂ ਬਹੁਤ ਲੰਬਾ ਹੈ, ਤਾਂ ਜੋ ਅਨਾਜ ਵਧੇ;
3. ਸੋਨੇ ਦੀ ਰਸਾਇਣਕ ਰਚਨਾ ਗੈਰ-ਵਾਜਬ ਹੈ;
4. ਸਾਧਾਰਨ ਹੀਟ-ਇਲਾਜ ਯੋਗ ਮਜ਼ਬੂਤ ਕਰਨ ਵਾਲੇ ਅਲੌਇਸਾਂ ਵਿੱਚ ਹੀਟ ਟ੍ਰੀਟਮੈਂਟ ਤੋਂ ਬਾਅਦ ਮੋਟੇ-ਦਾਣੇਦਾਰ ਰਿੰਗ ਹੁੰਦੇ ਹਨ, ਖਾਸ ਤੌਰ 'ਤੇ 6a02, 2a50 ਅਤੇ ਹੋਰ ਅਲਾਇਆਂ ਦੇ ਆਕਾਰ ਅਤੇ ਬਾਰ ਸਭ ਤੋਂ ਗੰਭੀਰ ਹੁੰਦੇ ਹਨ, ਜਿਨ੍ਹਾਂ ਨੂੰ ਖਤਮ ਨਹੀਂ ਕੀਤਾ ਜਾ ਸਕਦਾ ਅਤੇ ਸਿਰਫ਼ ਇੱਕ ਖਾਸ ਸੀਮਾ ਦੇ ਅੰਦਰ ਹੀ ਕੰਟਰੋਲ ਕੀਤਾ ਜਾ ਸਕਦਾ ਹੈ;
5. ਐਕਸਟਰਿਊਸ਼ਨ ਵਿਗਾੜ ਛੋਟਾ ਹੈ ਜਾਂ ਵਿਗਾੜ ਨਾਕਾਫੀ ਹੈ, ਜਾਂ ਨਾਜ਼ੁਕ ਵਿਗਾੜ ਸੀਮਾ ਵਿੱਚ ਹੈ, ਅਤੇ ਇੱਕ ਮੋਟੇ ਕ੍ਰਿਸਟਲ ਰਿੰਗ ਪੈਦਾ ਕਰਨਾ ਆਸਾਨ ਹੈ.
ਰੋਕਥਾਮ ਵਿਧੀ
1. ਐਕਸਟਰਿਊਸ਼ਨ ਸਿਲੰਡਰ ਦੀ ਅੰਦਰਲੀ ਕੰਧ ਨਿਰਵਿਘਨ ਅਤੇ ਸਾਫ਼ ਹੈ, ਐਕਸਟਰਿਊਸ਼ਨ ਦੌਰਾਨ ਰਗੜ ਨੂੰ ਘਟਾਉਣ ਲਈ ਇੱਕ ਪੂਰੀ ਅਲਮੀਨੀਅਮ ਸਲੀਵ ਬਣਾਉਂਦੀ ਹੈ;
2. ਵਿਗਾੜ ਜਿੰਨਾ ਸੰਭਵ ਹੋ ਸਕੇ ਪੂਰਾ ਅਤੇ ਇਕਸਾਰ ਹੋਣਾ ਚਾਹੀਦਾ ਹੈ, ਅਤੇ ਪ੍ਰਕਿਰਿਆ ਦੇ ਮਾਪਦੰਡ ਜਿਵੇਂ ਕਿ ਤਾਪਮਾਨ ਅਤੇ ਗਤੀ ਨੂੰ ਉਚਿਤ ਤੌਰ 'ਤੇ ਨਿਯੰਤਰਿਤ ਕੀਤਾ ਜਾਣਾ ਚਾਹੀਦਾ ਹੈ;
3. ਹੱਲ ਤੋਂ ਬਚੋ ਇਲਾਜ ਦਾ ਤਾਪਮਾਨ ਬਹੁਤ ਜ਼ਿਆਦਾ ਹੈ ਜਾਂ ਹੋਲਡਿੰਗ ਸਮਾਂ ਬਹੁਤ ਲੰਬਾ ਹੈ;
4. ਪੋਰਸ ਡਾਈ ਨਾਲ ਬਾਹਰ ਕੱਢਣਾ;
5. ਰਿਵਰਸ ਐਕਸਟ੍ਰੋਜ਼ਨ ਵਿਧੀ ਅਤੇ ਸਥਿਰ ਐਕਸਟਰੂਜ਼ਨ ਵਿਧੀ ਦੁਆਰਾ ਐਕਸਟਰੂਜ਼ਨ;
6. ਹੱਲ ਇਲਾਜ-ਡਰਾਇੰਗ-ਏਜਿੰਗ ਵਿਧੀ ਦੁਆਰਾ ਪੈਦਾ ਕੀਤਾ ਗਿਆ;
7. ਕੁੱਲ ਸੋਨੇ ਦੀ ਰਚਨਾ ਨੂੰ ਅਡਜੱਸਟ ਕਰੋ ਅਤੇ ਰੀਕ੍ਰਿਸਟਾਲਾਈਜ਼ੇਸ਼ਨ ਇਨਿਹਿਬੀਟਰੀ ਤੱਤ ਨੂੰ ਵਧਾਓ;
8. ਉੱਚ ਤਾਪਮਾਨ ਐਕਸਟਰਿਊਸ਼ਨ ਦੀ ਵਰਤੋਂ ਕਰੋ;
9. ਕੁਝ ਮਿਸ਼ਰਤ ਇੰਦਰੀਆਂ ਇਕਸਾਰ ਨਹੀਂ ਹੁੰਦੀਆਂ ਹਨ, ਅਤੇ ਬਾਹਰ ਕੱਢਣ ਦੌਰਾਨ ਮੋਟੇ ਅਨਾਜ ਦੀ ਰਿੰਗ ਘੱਟ ਹੁੰਦੀ ਹੈ।
III, ਲੇਅਰਡ
ਇਹ ਚਮੜੀ ਦੇ ਡੈਲੇਮੀਨੇਸ਼ਨ ਨੁਕਸ ਦਾ ਗਠਨ ਹੁੰਦਾ ਹੈ ਜਦੋਂ ਧਾਤ ਦਾ ਪ੍ਰਵਾਹ ਮੁਕਾਬਲਤਨ ਇਕਸਾਰ ਹੁੰਦਾ ਹੈ, ਅਤੇ ਇਨਗੋਟ ਦੀ ਸਤਹ ਉੱਲੀ ਅਤੇ ਅਗਲੇ ਸਿਰੇ ਦੇ ਲਚਕੀਲੇ ਜ਼ੋਨ ਦੇ ਵਿਚਕਾਰ ਇੰਟਰਫੇਸ ਦੇ ਨਾਲ ਉਤਪਾਦ ਵਿੱਚ ਵਹਿੰਦੀ ਹੈ।ਟ੍ਰਾਂਸਵਰਸ ਲੋ-ਵੱਡਰੀਕਰਨ ਟੈਸਟ ਟੁਕੜੇ 'ਤੇ, ਇਹ ਪ੍ਰਤੀਤ ਹੁੰਦਾ ਹੈ ਕਿ ਕਰਾਸ-ਸੈਕਸ਼ਨ ਦੇ ਕਿਨਾਰੇ 'ਤੇ ਵੱਖ-ਵੱਖ ਲੇਅਰਾਂ ਦਾ ਨੁਕਸ ਹੈ।
ਪੱਧਰੀਕਰਨ ਦਾ ਮੁੱਖ ਕਾਰਨ
1. ਇੰਗੋਟ ਦੀ ਸਤ੍ਹਾ 'ਤੇ ਧੂੜ ਹੈ ਜਾਂ ਇਨਗੌਟ ਵਿਚ ਕਾਰ ਦੀ ਚਮੜੀ, ਧਾਤ ਦੇ ਟਿਊਮਰ, ਆਦਿ ਦੀ ਬਜਾਏ ਵੱਡੇ ਸੈਗਰੀਗੇਟ ਐਗਰੀਗੇਟਸ ਹਨ, ਜੋ ਕਿ ਪਰਤਾਂ ਬਣਾਉਣ ਲਈ ਆਸਾਨ ਹਨ;
2. ਖਾਲੀ ਦੀ ਸਤਹ 'ਤੇ burrs ਹਨ ਜਾਂ ਗੰਦਗੀ ਜਿਵੇਂ ਕਿ ਤੇਲ ਦੇ ਧੱਬੇ, ਬਰਾ, ਆਦਿ, ਜੋ ਬਾਹਰ ਕੱਢਣ ਤੋਂ ਪਹਿਲਾਂ ਸਾਫ਼ ਨਹੀਂ ਕੀਤੇ ਜਾਂਦੇ ਹਨ;
3. ਡਾਈ ਹੋਲ ਦੀ ਸਥਿਤੀ ਗੈਰ-ਵਾਜਬ ਹੈ, ਐਕਸਟਰਿਊਸ਼ਨ ਸਿਲੰਡਰ ਦੇ ਕਿਨਾਰੇ ਦੇ ਨੇੜੇ;
4. ਐਕਸਟਰਿਊਸ਼ਨ ਟੂਲ ਗੰਭੀਰਤਾ ਨਾਲ ਖਰਾਬ ਹੈ ਜਾਂ ਐਕਸਟਰਿਊਸ਼ਨ ਸਿਲੰਡਰ ਦੀ ਝਾੜੀ ਵਿੱਚ ਗੰਦਗੀ ਹੈ, ਜਿਸ ਨੂੰ ਸਮੇਂ ਸਿਰ ਸਾਫ਼ ਅਤੇ ਬਦਲਿਆ ਨਹੀਂ ਜਾ ਸਕਦਾ ਹੈ;
5. ਐਕਸਟਰਿਊਸ਼ਨ ਪੈਡ ਦਾ ਵਿਆਸ ਅੰਤਰ ਬਹੁਤ ਵੱਡਾ ਹੈ;
6. ਐਕਸਟਰਿਊਸ਼ਨ ਸਿਲੰਡਰ ਦਾ ਤਾਪਮਾਨ ਇੰਗੋਟ ਨਾਲੋਂ ਬਹੁਤ ਜ਼ਿਆਦਾ ਹੁੰਦਾ ਹੈ।
ਰੋਕਥਾਮ ਵਿਧੀ
1. ਮੋਲਡਾਂ ਦਾ ਵਾਜਬ ਡਿਜ਼ਾਈਨ, ਸਮੇਂ ਸਿਰ ਨਿਰੀਖਣ ਅਤੇ ਅਯੋਗ ਸਾਧਨਾਂ ਦੀ ਬਦਲੀ;
2. ਭੱਠੀ ਵਿੱਚ ਅਯੋਗ ਇਨਗੋਟਸ ਸਥਾਪਿਤ ਨਹੀਂ ਕੀਤੇ ਜਾਂਦੇ ਹਨ;
3. ਬਚੀ ਹੋਈ ਸਮੱਗਰੀ ਨੂੰ ਕੱਟਣ ਤੋਂ ਬਾਅਦ, ਇਸਨੂੰ ਲੁਬਰੀਕੇਟਿੰਗ ਤੇਲ ਨਾਲ ਚਿਪਕਾਏ ਬਿਨਾਂ ਸਾਫ਼ ਕੀਤਾ ਜਾਣਾ ਚਾਹੀਦਾ ਹੈ;
4. ਐਕਸਟਰਿਊਸ਼ਨ ਸਿਲੰਡਰ ਦੀ ਲਾਈਨਿੰਗ ਨੂੰ ਬਰਕਰਾਰ ਰੱਖੋ, ਜਾਂ ਗੈਸਕੇਟ ਨਾਲ ਸਮੇਂ ਸਿਰ ਲਾਈਨਿੰਗ ਨੂੰ ਸਾਫ਼ ਕਰੋ।
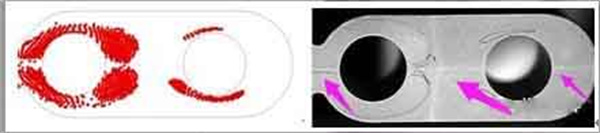
IV.ਮਾੜੀ ਵੈਲਡਿੰਗ
ਵੇਲਡ 'ਤੇ ਸਪਲਿਟ ਡਾਈ ਦੁਆਰਾ ਬਾਹਰ ਕੱਢੇ ਗਏ ਖੋਖਲੇ ਉਤਪਾਦ ਦੀ ਵੈਲਡ ਡੀਲਾਮੀਨੇਸ਼ਨ ਜਾਂ ਅਧੂਰੀ ਵੈਲਡਿੰਗ ਦੀ ਘਟਨਾ ਨੂੰ ਖਰਾਬ ਵੈਲਡਿੰਗ ਕਿਹਾ ਜਾਂਦਾ ਹੈ।
ਗਰੀਬ ਵੈਲਡਿੰਗ ਦਾ ਮੁੱਖ ਕਾਰਨ
1. ਐਕਸਟਰੂਜ਼ਨ ਗੁਣਾਂਕ ਛੋਟਾ ਹੈ, ਐਕਸਟਰੂਜ਼ਨ ਦਾ ਤਾਪਮਾਨ ਘੱਟ ਹੈ, ਅਤੇ ਐਕਸਟਰੂਜ਼ਨ ਦੀ ਗਤੀ ਤੇਜ਼ ਹੈ;
2. ਐਕਸਟਰਿਊਸ਼ਨ ਉੱਨ ਜਾਂ ਸੰਦ ਸਾਫ਼ ਨਹੀਂ ਹਨ;
3. ਉੱਲੀ ਨੂੰ ਤੇਲ;
4. ਅਣਉਚਿਤ ਮੋਲਡ ਡਿਜ਼ਾਈਨ, ਨਾਕਾਫ਼ੀ ਜਾਂ ਅਸੰਤੁਲਿਤ ਹਾਈਡ੍ਰੋਸਟੈਟਿਕ ਦਬਾਅ, ਸ਼ੰਟ ਹੋਲਾਂ ਦਾ ਗੈਰ-ਵਾਜਬ ਡਿਜ਼ਾਈਨ;
5. ਪਿੰਜੀ ਦੀ ਸਤ੍ਹਾ 'ਤੇ ਤੇਲ ਦਾ ਦਾਗ ਹੁੰਦਾ ਹੈ।
ਰੋਕਥਾਮ ਵਿਧੀ
1. ਸਹੀ ਢੰਗ ਨਾਲ ਐਕਸਟਰੂਜ਼ਨ ਗੁਣਾਂਕ, ਐਕਸਟਰੂਜ਼ਨ ਤਾਪਮਾਨ ਅਤੇ ਬਾਹਰ ਕੱਢਣ ਦੀ ਗਤੀ ਵਧਾਓ;
2. ਉਚਿਤ ਡਿਜ਼ਾਈਨ ਅਤੇ ਮੋਲਡ ਦਾ ਨਿਰਮਾਣ;
3. ਐਕਸਟਰੂਜ਼ਨ ਸਿਲੰਡਰ ਅਤੇ ਐਕਸਟਰੂਜ਼ਨ ਗੈਸਕੇਟ ਨੂੰ ਤੇਲ ਨਹੀਂ ਲਗਾਇਆ ਜਾਂਦਾ ਅਤੇ ਸਾਫ਼ ਰੱਖਿਆ ਜਾਂਦਾ ਹੈ;
4. ਸਾਫ਼ ਸਤ੍ਹਾ ਦੇ ਨਾਲ ਇਨਗੋਟਸ ਦੀ ਵਰਤੋਂ ਕਰੋ।
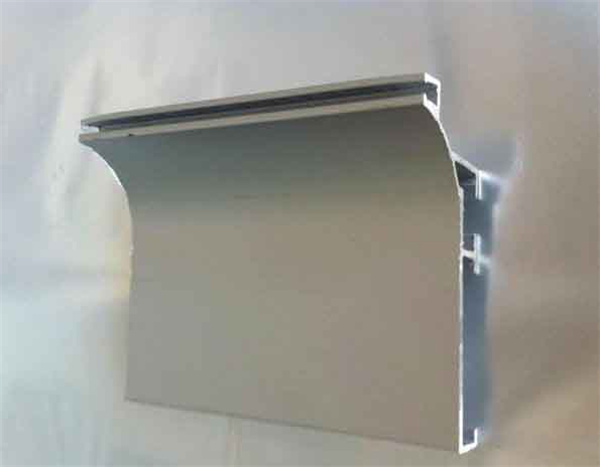
V. ਐਕਸਟਰਿਊਸ਼ਨ ਚੀਰ
ਇਹ ਐਕਸਟਰੂਡ ਉਤਪਾਦ ਦੇ ਟਰਾਂਸਵਰਸ ਟੈਸਟ ਟੁਕੜੇ ਦੇ ਕਿਨਾਰੇ 'ਤੇ ਇੱਕ ਛੋਟੀ ਜਿਹੀ ਚਾਪ-ਆਕਾਰ ਦੀ ਦਰਾੜ ਹੈ, ਅਤੇ ਇਸਦੀ ਲੰਮੀ ਦਿਸ਼ਾ ਦੇ ਨਾਲ ਇੱਕ ਖਾਸ ਕੋਣ 'ਤੇ ਸਮੇਂ-ਸਮੇਂ 'ਤੇ ਕ੍ਰੈਕਿੰਗ, ਜੋ ਕਿ ਹਲਕੇ ਮਾਮਲਿਆਂ ਵਿੱਚ ਐਪੀਡਰਿਮਸ ਦੇ ਹੇਠਾਂ ਲੁਕੀ ਹੋਈ ਹੈ, ਅਤੇ ਬਾਹਰੀ ਪਰਤ ਵਿੱਚ ਸੀਰੇਟਿਡ ਚੀਰ। ਗੰਭੀਰ ਮਾਮਲਿਆਂ ਵਿੱਚ, ਜੋ ਧਾਤ ਦੀ ਨਿਰੰਤਰਤਾ ਨੂੰ ਗੰਭੀਰਤਾ ਨਾਲ ਨੁਕਸਾਨ ਪਹੁੰਚਾਏਗਾ।ਐਕਸਟਰਿਊਸ਼ਨ ਚੀਰ ਉਦੋਂ ਬਣਦੀ ਹੈ ਜਦੋਂ ਬਾਹਰ ਕੱਢਣ ਦੀ ਪ੍ਰਕਿਰਿਆ ਦੌਰਾਨ ਡਾਈ ਦੀਵਾਰ ਦੇ ਬਹੁਤ ਜ਼ਿਆਦਾ ਸਮੇਂ-ਸਮੇਂ ਤੇ ਤਣਾਅ ਨਾਲ ਧਾਤ ਦੀ ਸਤ੍ਹਾ ਨੂੰ ਪਾਟ ਜਾਂਦਾ ਹੈ।
ਐਕਸਟਰਿਊਸ਼ਨ ਚੀਰ ਦਾ ਮੁੱਖ ਕਾਰਨ
1. ਬਾਹਰ ਕੱਢਣ ਦੀ ਗਤੀ ਬਹੁਤ ਤੇਜ਼ ਹੈ;
2. ਬਾਹਰ ਕੱਢਣ ਦਾ ਤਾਪਮਾਨ ਬਹੁਤ ਜ਼ਿਆਦਾ ਹੈ;
3. ਬਾਹਰ ਕੱਢਣ ਦੀ ਗਤੀ ਬਹੁਤ ਜ਼ਿਆਦਾ ਉਤਰਾਅ-ਚੜ੍ਹਾਅ ਕਰਦੀ ਹੈ;
4. extruded ਉੱਨ ਦਾ ਤਾਪਮਾਨ ਬਹੁਤ ਜ਼ਿਆਦਾ ਹੈ;
5. ਜਦੋਂ ਪੋਰਸ ਡਾਈ ਨੂੰ ਬਾਹਰ ਕੱਢਿਆ ਜਾਂਦਾ ਹੈ, ਤਾਂ ਮਰਨ ਦਾ ਪ੍ਰਬੰਧ ਕੇਂਦਰ ਦੇ ਬਹੁਤ ਨੇੜੇ ਹੁੰਦਾ ਹੈ, ਤਾਂ ਜੋ ਕੇਂਦਰੀ ਧਾਤ ਦੀ ਸਪਲਾਈ ਨਾਕਾਫ਼ੀ ਹੋਵੇ, ਤਾਂ ਜੋ ਕੇਂਦਰ ਅਤੇ ਕਿਨਾਰੇ ਦੇ ਵਹਾਅ ਦੀ ਦਰ ਵਿੱਚ ਅੰਤਰ ਬਹੁਤ ਵੱਡਾ ਹੋਵੇ;
6. ਇਨਗੋਟ ਹੋਮੋਜਨਾਈਜ਼ੇਸ਼ਨ ਐਨੀਲਿੰਗ ਚੰਗੀ ਨਹੀਂ ਹੈ।
ਰੋਕਥਾਮ ਵਿਧੀ
1. ਵੱਖ-ਵੱਖ ਹੀਟਿੰਗ ਅਤੇ ਐਕਸਟਰਿਊਸ਼ਨ ਵਿਸ਼ੇਸ਼ਤਾਵਾਂ ਨੂੰ ਸਖਤੀ ਨਾਲ ਲਾਗੂ ਕਰੋ;
2. ਸਾਧਾਰਨ ਕਾਰਵਾਈ ਨੂੰ ਯਕੀਨੀ ਬਣਾਉਣ ਲਈ ਯੰਤਰਾਂ ਅਤੇ ਸਾਜ਼-ਸਾਮਾਨ ਦੀ ਵਾਰ-ਵਾਰ ਜਾਂਚ;
3. ਮੋਲਡ ਡਿਜ਼ਾਈਨ ਨੂੰ ਸੋਧੋ ਅਤੇ ਧਿਆਨ ਨਾਲ ਇਸ ਦੀ ਪ੍ਰਕਿਰਿਆ ਕਰੋ, ਖਾਸ ਤੌਰ 'ਤੇ ਮੋਲਡ ਬ੍ਰਿਜ, ਵੈਲਡਿੰਗ ਰੂਮ ਅਤੇ ਕਿਨਾਰੇ ਦੇ ਘੇਰੇ ਦਾ ਡਿਜ਼ਾਈਨ ਵਾਜਬ ਹੋਣਾ ਚਾਹੀਦਾ ਹੈ;
4. ਉੱਚ ਮੈਗਨੀਸ਼ੀਅਮ ਅਲਮੀਨੀਅਮ ਮਿਸ਼ਰਤ ਵਿੱਚ ਸੋਡੀਅਮ ਸਮੱਗਰੀ ਨੂੰ ਘੱਟ ਤੋਂ ਘੱਟ ਕਰੋ;
5. ਇਸਦੀ ਪਲਾਸਟਿਕਤਾ ਅਤੇ ਇਕਸਾਰਤਾ ਨੂੰ ਬਿਹਤਰ ਬਣਾਉਣ ਲਈ ਪਿੰਜਰੇ ਨੂੰ ਸਮਰੂਪ ਕੀਤਾ ਜਾਂਦਾ ਹੈ ਅਤੇ ਐਨੀਲਡ ਕੀਤਾ ਜਾਂਦਾ ਹੈ।
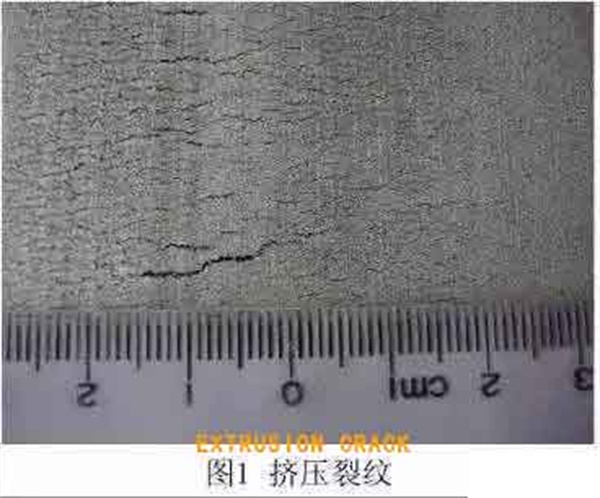
VI.ਬੁਲਬੁਲੇ
ਸਥਾਨਕ ਚਮੜੀ ਦੀ ਧਾਤ ਬੇਸ ਧਾਤੂ ਤੋਂ ਲਗਾਤਾਰ ਜਾਂ ਲਗਾਤਾਰ ਵੱਖ ਕੀਤੀ ਜਾਂਦੀ ਹੈ, ਅਤੇ ਇਹ ਇੱਕ ਗੋਲਾਕਾਰ ਸਿੰਗਲ ਜਾਂ ਸਟ੍ਰਿਪ-ਆਕਾਰ ਦੇ ਕੈਵਿਟੀ ਵਿੱਚ ਉਭਾਰਿਆ ਨੁਕਸ ਦੇ ਰੂਪ ਵਿੱਚ ਪ੍ਰਗਟ ਹੁੰਦਾ ਹੈ, ਜਿਸਨੂੰ ਬੁਲਬੁਲਾ ਕਿਹਾ ਜਾਂਦਾ ਹੈ।
ਬੁਲਬਲੇ ਦਾ ਮੁੱਖ ਕਾਰਨ
1. ਬਾਹਰ ਕੱਢਣ ਵੇਲੇ, ਐਕਸਟਰੂਜ਼ਨ ਸਿਲੰਡਰ ਅਤੇ ਐਕਸਟਰੂਜ਼ਨ ਪੈਡ ਵਿੱਚ ਨਮੀ ਅਤੇ ਤੇਲ ਵਰਗੀ ਗੰਦਗੀ ਹੁੰਦੀ ਹੈ;
2. ਐਕਸਟਰਿਊਸ਼ਨ ਸਿਲੰਡਰ ਦੇ ਪਹਿਨਣ ਦੇ ਕਾਰਨ, ਐਕਸਟਰਿਊਸ਼ਨ ਦੌਰਾਨ ਖਰਾਬ ਹਿੱਸੇ ਅਤੇ ਇਨਗੋਟ ਦੇ ਵਿਚਕਾਰ ਹਵਾ ਧਾਤ ਦੀ ਸਤ੍ਹਾ ਵਿੱਚ ਦਾਖਲ ਹੁੰਦੀ ਹੈ;
3. ਲੁਬਰੀਕੈਂਟ ਵਿੱਚ ਨਮੀ ਹੁੰਦੀ ਹੈ;
4. ਪਿੰਜਰੇ ਦੀ ਬਣਤਰ ਆਪਣੇ ਆਪ ਵਿੱਚ ਢਿੱਲੀ ਅਤੇ ਪੋਰੋਸਿਟੀ ਨੁਕਸ ਹੈ;
5. ਗਰਮੀ ਦੇ ਇਲਾਜ ਦਾ ਤਾਪਮਾਨ ਬਹੁਤ ਜ਼ਿਆਦਾ ਹੈ, ਹੋਲਡਿੰਗ ਸਮਾਂ ਬਹੁਤ ਲੰਬਾ ਹੈ, ਅਤੇ ਭੱਠੀ ਵਿੱਚ ਵਾਯੂਮੰਡਲ ਦੀ ਨਮੀ ਜ਼ਿਆਦਾ ਹੈ;
6. ਉਤਪਾਦ ਵਿੱਚ ਹਾਈਡਰੋਜਨ ਸਮੱਗਰੀ ਬਹੁਤ ਜ਼ਿਆਦਾ ਹੈ;
7. ਐਕਸਟਰਿਊਸ਼ਨ ਸਿਲੰਡਰ ਦਾ ਤਾਪਮਾਨ ਅਤੇ ਇੰਗਟ ਦਾ ਤਾਪਮਾਨ ਬਹੁਤ ਜ਼ਿਆਦਾ ਹੈ।
ਰੋਕਥਾਮ ਵਿਧੀ
1. ਟੂਲਸ ਅਤੇ ਇਨਗੋਟਸ ਦੀਆਂ ਸਤਹਾਂ ਨੂੰ ਸਾਫ਼, ਨਿਰਵਿਘਨ ਅਤੇ ਸੁੱਕਾ ਰੱਖਿਆ ਜਾਣਾ ਚਾਹੀਦਾ ਹੈ;
2. ਐਕਸਟਰੂਜ਼ਨ ਸਿਲੰਡਰ ਅਤੇ ਐਕਸਟਰੂਜ਼ਨ ਗੈਸਕੇਟ ਦੇ ਮੇਲ ਖਾਂਦੇ ਆਕਾਰ ਨੂੰ ਉਚਿਤ ਰੂਪ ਵਿੱਚ ਡਿਜ਼ਾਈਨ ਕਰੋ, ਟੂਲ ਦੇ ਆਕਾਰ ਦੀ ਵਾਰ-ਵਾਰ ਜਾਂਚ ਕਰੋ, ਜਦੋਂ ਇੱਕ ਵੱਡਾ ਢਿੱਡ ਹੋਵੇ ਤਾਂ ਐਕਸਟਰੂਜ਼ਨ ਸਿਲੰਡਰ ਦੀ ਸਮੇਂ ਸਿਰ ਮੁਰੰਮਤ ਕਰੋ, ਅਤੇ ਐਕਸਟਰੂਜ਼ਨ ਗੈਸਕੇਟ ਸਹਿਣਸ਼ੀਲਤਾ ਤੋਂ ਬਾਹਰ ਨਹੀਂ ਹੋਣੀ ਚਾਹੀਦੀ;
3. ਯਕੀਨੀ ਬਣਾਓ ਕਿ ਲੁਬਰੀਕੈਂਟ ਸਾਫ਼ ਅਤੇ ਸੁੱਕਾ ਹੈ;
4. ਬਾਹਰ ਕੱਢਣ ਦੀ ਪ੍ਰਕਿਰਿਆ ਦੀ ਕਾਰਵਾਈ ਦੀ ਪ੍ਰਕਿਰਿਆ ਦੀ ਸਖਤੀ ਨਾਲ ਪਾਲਣਾ ਕਰੋ, ਸਮੇਂ ਸਿਰ ਨਿਕਾਸ ਕਰੋ, ਸਹੀ ਢੰਗ ਨਾਲ ਕੱਟੋ, ਤੇਲ ਨਾ ਲਗਾਓ, ਬਾਕੀ ਬਚੀਆਂ ਸਮੱਗਰੀਆਂ ਨੂੰ ਪੂਰੀ ਤਰ੍ਹਾਂ ਹਟਾਓ, ਖਾਲੀ ਥਾਂਵਾਂ ਅਤੇ ਮੋਲਡਾਂ ਨੂੰ ਸਾਫ਼ ਰੱਖੋ ਅਤੇ ਪ੍ਰਦੂਸ਼ਿਤ ਨਾ ਕਰੋ।
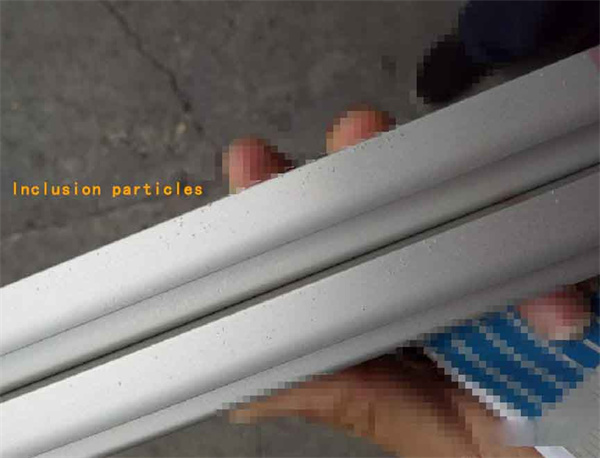
VII.ਪੀਲਿੰਗ
ਇਹ ਚਮੜੀ ਦੀ ਧਾਤ ਅਤੇ ਅਲਮੀਨੀਅਮ ਮਿਸ਼ਰਤ ਐਕਸਟਰਿਊਸ਼ਨ ਉਤਪਾਦ ਦੀ ਬੇਸ ਮੈਟਲ ਦੇ ਵਿਚਕਾਰ ਸਥਾਨਕ ਵੱਖ ਹੋਣ ਦੀ ਘਟਨਾ ਹੈ।
ਛਿੱਲਣ ਦਾ ਮੁੱਖ ਕਾਰਨ
1. ਜਦੋਂ ਮਿਸ਼ਰਤ ਨੂੰ ਬਦਲਿਆ ਜਾਂਦਾ ਹੈ ਅਤੇ ਬਾਹਰ ਕੱਢਿਆ ਜਾਂਦਾ ਹੈ, ਤਾਂ ਐਕਸਟਰਿਊਸ਼ਨ ਸਿਲੰਡਰ ਦੀ ਅੰਦਰਲੀ ਕੰਧ ਅਸਲੀ ਧਾਤ ਦੁਆਰਾ ਬਣਾਈ ਝਾੜੀ ਨਾਲ ਚਿਪਕ ਜਾਂਦੀ ਹੈ, ਜਿਸ ਨੂੰ ਸਹੀ ਢੰਗ ਨਾਲ ਸਾਫ਼ ਨਹੀਂ ਕੀਤਾ ਜਾਂਦਾ ਹੈ;
2. ਐਕਸਟਰੂਜ਼ਨ ਸਿਲੰਡਰ ਅਤੇ ਐਕਸਟਰੂਜ਼ਨ ਪੈਡ ਸਹੀ ਤਰ੍ਹਾਂ ਨਾਲ ਮੇਲ ਨਹੀਂ ਖਾਂਦੇ, ਅਤੇ ਐਕਸਟਰੂਜ਼ਨ ਸਿਲੰਡਰ ਦੀ ਅੰਦਰਲੀ ਕੰਧ ਸਥਾਨਕ ਬਚੀ ਹੋਈ ਧਾਤ ਨਾਲ ਕਤਾਰਬੱਧ ਹੈ;
3. ਇਹ ਐਕਸਟਰੂਜ਼ਨ ਸਿਲੰਡਰ ਲੁਬਰੀਕੇਟਿੰਗ ਦੁਆਰਾ ਬਾਹਰ ਕੱਢਿਆ ਜਾਂਦਾ ਹੈ;
4. ਡਾਈ ਹੋਲ 'ਤੇ ਧਾਤ ਹੈ ਜਾਂ ਡਾਈ ਦੀ ਵਰਕਿੰਗ ਬੈਲਟ ਬਹੁਤ ਲੰਬੀ ਹੈ।
ਰੋਕਥਾਮ ਵਿਧੀ
1. ਮਿਸ਼ਰਤ ਨੂੰ ਕੱਢਣ ਵੇਲੇ ਐਕਸਟਰਿਊਸ਼ਨ ਸਿਲੰਡਰ ਨੂੰ ਚੰਗੀ ਤਰ੍ਹਾਂ ਸਾਫ਼ ਕਰੋ;
2. ਐਕਸਟਰੂਜ਼ਨ ਸਿਲੰਡਰ ਅਤੇ ਐਕਸਟਰੂਜ਼ਨ ਗੈਸਕੇਟ ਦੇ ਮੇਲ ਖਾਂਦੇ ਆਕਾਰ ਨੂੰ ਉਚਿਤ ਰੂਪ ਵਿੱਚ ਡਿਜ਼ਾਈਨ ਕਰੋ, ਟੂਲ ਦੇ ਆਕਾਰ ਦੀ ਵਾਰ-ਵਾਰ ਜਾਂਚ ਕਰੋ, ਅਤੇ ਐਕਸਟਰੂਜ਼ਨ ਗੈਸਕਟ ਸਹਿਣਸ਼ੀਲਤਾ ਤੋਂ ਬਾਹਰ ਨਹੀਂ ਹੋ ਸਕਦਾ;
3. ਸਮੇਂ ਸਿਰ ਉੱਲੀ 'ਤੇ ਬਚੀ ਹੋਈ ਧਾਤ ਨੂੰ ਸਾਫ਼ ਕਰੋ।
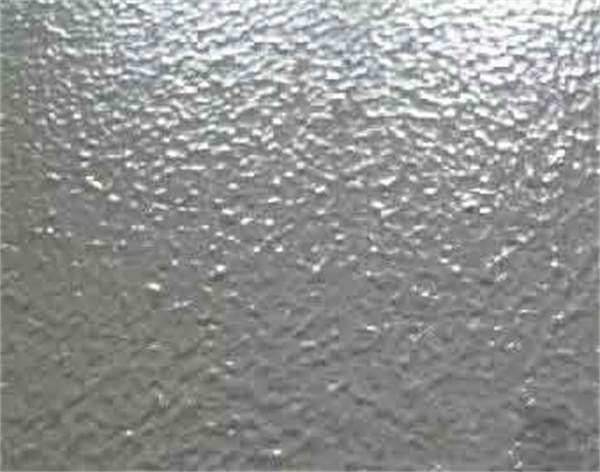
VIII.ਸਕਰੈਚ
ਸਾਪੇਖਿਕ ਸਲਾਈਡਿੰਗ ਦੌਰਾਨ ਤਿੱਖੀਆਂ ਵਸਤੂਆਂ ਅਤੇ ਉਤਪਾਦ ਦੀ ਸਤਹ ਦੇ ਵਿਚਕਾਰ ਸੰਪਰਕ ਦੇ ਕਾਰਨ ਇੱਕ-ਧਾਰੀ ਵਾਲੇ ਮਕੈਨੀਕਲ ਦਾਗ ਨੂੰ ਸਕ੍ਰੈਚ ਕਿਹਾ ਜਾਂਦਾ ਹੈ।
ਖੁਰਚਣ ਦਾ ਮੁੱਖ ਕਾਰਨ
1. ਔਜ਼ਾਰਾਂ ਦੀ ਅਣਉਚਿਤ ਅਸੈਂਬਲੀ, ਨਿਰਵਿਘਨ ਗਾਈਡਾਂ ਅਤੇ ਵਰਕਟੇਬਲ, ਤਿੱਖੇ ਕੋਨੇ ਜਾਂ ਵਿਦੇਸ਼ੀ ਵਸਤੂਆਂ, ਆਦਿ;
2. ਮੋਲਡ ਵਰਕਿੰਗ ਬੈਲਟ 'ਤੇ ਮੈਟਲ ਚਿਪਸ ਹਨ ਜਾਂ ਮੋਲਡ ਵਰਕਿੰਗ ਬੈਲਟ ਖਰਾਬ ਹੈ;
3. ਲੁਬਰੀਕੇਟਿੰਗ ਤੇਲ ਵਿੱਚ ਰੇਤ ਜਾਂ ਟੁੱਟੀਆਂ ਧਾਤ ਦੀਆਂ ਚਿਪਸ ਹਨ;
4. ਢੋਆ-ਢੁਆਈ ਅਤੇ ਅਣਉਚਿਤ ਫੈਲਾਉਣ ਵਾਲੇ ਦੌਰਾਨ ਗਲਤ ਕਾਰਵਾਈ।
ਰੋਕਥਾਮ ਵਿਧੀ
1. ਸਮੇਂ ਸਿਰ ਮੋਲਡ ਵਰਕਿੰਗ ਬੈਲਟ ਦੀ ਜਾਂਚ ਕਰੋ ਅਤੇ ਪਾਲਿਸ਼ ਕਰੋ;
2. ਉਤਪਾਦ ਦੇ ਆਊਟਫਲੋ ਚੈਨਲ ਦੀ ਜਾਂਚ ਕਰੋ, ਇਹ ਨਿਰਵਿਘਨ ਹੋਣਾ ਚਾਹੀਦਾ ਹੈ, ਅਤੇ ਗਾਈਡ ਮਾਰਗ ਨੂੰ ਸਹੀ ਤਰ੍ਹਾਂ ਲੁਬਰੀਕੇਟ ਕੀਤਾ ਜਾ ਸਕਦਾ ਹੈ;
3. ਹੈਂਡਲਿੰਗ ਦੌਰਾਨ ਮਕੈਨੀਕਲ ਰਗੜਨ ਅਤੇ ਖੁਰਕਣ ਤੋਂ ਰੋਕੋ।
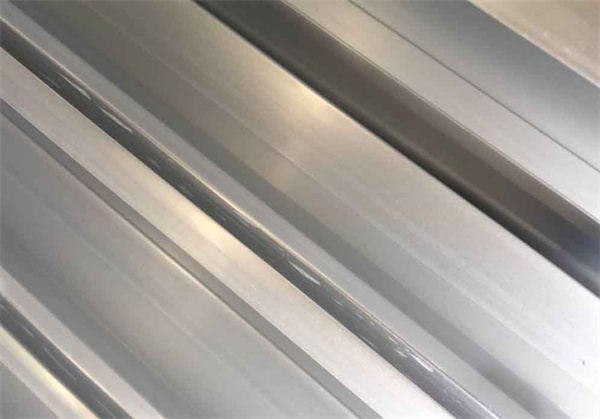
IX.ਬੰਪ
ਉਤਪਾਦਾਂ ਦੀ ਸਤ੍ਹਾ 'ਤੇ ਬਣੇ ਦਾਗ ਜਾਂ ਹੋਰ ਵਸਤੂਆਂ ਨਾਲ ਟਕਰਾਉਣ ਵਾਲੇ ਉਤਪਾਦਾਂ ਨੂੰ ਬੰਪ ਇੰਜਰੀ ਕਿਹਾ ਜਾਂਦਾ ਹੈ।
ਝੁਲਸਣ ਦਾ ਮੁੱਖ ਕਾਰਨ
1. ਵਰਕਬੈਂਚ ਅਤੇ ਸਮਗਰੀ ਰੈਕ ਦੀ ਬਣਤਰ ਗੈਰ-ਵਾਜਬ ਹੈ;
2. ਸਮੱਗਰੀ ਦੀਆਂ ਟੋਕਰੀਆਂ, ਸਮੱਗਰੀ ਰੈਕ, ਆਦਿ ਦੀ ਗਲਤ ਧਾਤ ਦੀ ਸੁਰੱਖਿਆ;
3. ਕੰਮ ਕਰਦੇ ਸਮੇਂ ਇਸ ਨੂੰ ਸਾਵਧਾਨੀ ਨਾਲ ਨਾ ਸੰਭਾਲੋ।
ਰੋਕਥਾਮ ਵਿਧੀ
1. ਧਿਆਨ ਨਾਲ ਕਾਰਵਾਈ, ਦੇਖਭਾਲ ਨਾਲ ਹੈਂਡਲ;
2. ਤਿੱਖੇ ਕੋਨਿਆਂ ਨੂੰ ਪੀਸ ਲਓ, ਅਤੇ ਟੋਕਰੀ ਅਤੇ ਰੈਕ ਨੂੰ ਡੰਨੇਜ ਅਤੇ ਨਰਮ ਸਮੱਗਰੀ ਨਾਲ ਢੱਕੋ।
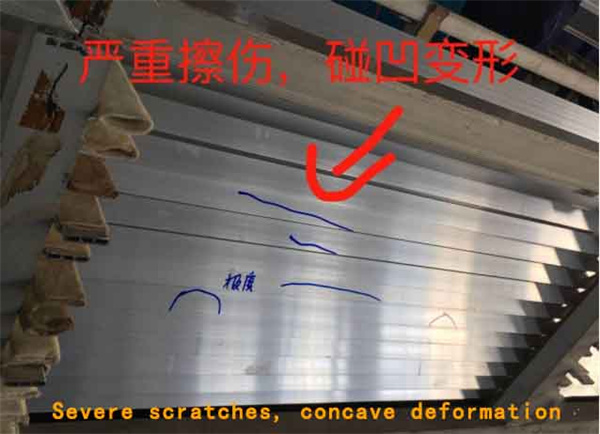
X. ਸਕ੍ਰੈਚਸ
ਬਾਹਰ ਕੱਢੇ ਉਤਪਾਦ ਦੀ ਸਤ੍ਹਾ ਦੇ ਕਿਨਾਰਿਆਂ ਜਾਂ ਹੋਰ ਵਸਤੂਆਂ ਦੀਆਂ ਸਤਹਾਂ ਦੇ ਸੰਪਰਕ ਵਿੱਚ ਆਉਣ ਤੋਂ ਬਾਅਦ ਸਾਪੇਖਿਕ ਸਲਾਈਡਿੰਗ ਜਾਂ ਵਿਸਥਾਪਨ ਦੇ ਕਾਰਨ ਉਤਪਾਦ ਦੀ ਸਤ੍ਹਾ 'ਤੇ ਬੰਡਲਾਂ ਵਿੱਚ ਵੰਡੇ ਗਏ ਦਾਗਾਂ ਨੂੰ ਸਕ੍ਰੈਚ ਕਿਹਾ ਜਾਂਦਾ ਹੈ।
ਖੁਰਚਣ ਦਾ ਮੁੱਖ ਕਾਰਨ
1. ਉੱਲੀ ਨੂੰ ਗੰਭੀਰਤਾ ਨਾਲ ਪਹਿਨਿਆ ਜਾਂਦਾ ਹੈ;
2. ਇੰਗੋਟ ਦੇ ਉੱਚ ਤਾਪਮਾਨ ਦੇ ਕਾਰਨ, ਡਾਈ ਹੋਲ ਅਲਮੀਨੀਅਮ ਨਾਲ ਚਿਪਕ ਜਾਂਦਾ ਹੈ ਜਾਂ ਡਾਈ ਹੋਲ ਵਰਕਿੰਗ ਬੈਲਟ ਨੂੰ ਨੁਕਸਾਨ ਪਹੁੰਚਦਾ ਹੈ;
3. ਗੰਦਗੀ ਜਿਵੇਂ ਕਿ ਗ੍ਰੈਫਾਈਟ ਅਤੇ ਤੇਲ ਐਕਸਟਰਿਊਸ਼ਨ ਸਿਲੰਡਰ ਵਿੱਚ ਡਿੱਗਦੇ ਹਨ;
4. ਉਤਪਾਦ ਇੱਕ ਦੂਜੇ ਦੇ ਨਾਲ ਚਲਦੇ ਹਨ, ਤਾਂ ਜੋ ਸਤ੍ਹਾ ਨੂੰ ਖੁਰਚਿਆ ਜਾਵੇ ਅਤੇ ਐਕਸਟਰਿਊਸ਼ਨ ਵਹਾਅ ਅਸਮਾਨ ਹੈ, ਜਿਸ ਨਾਲ ਉਤਪਾਦ ਇੱਕ ਸਿੱਧੀ ਲਾਈਨ ਵਿੱਚ ਨਹੀਂ ਵਹਿੰਦੇ ਹਨ, ਨਤੀਜੇ ਵਜੋਂ ਸਮੱਗਰੀ ਅਤੇ ਗਾਈਡ ਮਾਰਗ ਅਤੇ ਵਰਕਟੇਬਲ ਦੇ ਵਿਚਕਾਰ ਖੁਰਚ ਜਾਂਦੇ ਹਨ।
ਰੋਕਥਾਮ ਵਿਧੀ
1. ਸਮੇਂ ਸਿਰ ਅਯੋਗ ਮੋਲਡਾਂ ਦੀ ਜਾਂਚ ਕਰੋ ਅਤੇ ਬਦਲੋ;
2. ਉੱਨ ਦੇ ਹੀਟਿੰਗ ਤਾਪਮਾਨ ਨੂੰ ਕੰਟਰੋਲ ਕਰੋ;
3. ਯਕੀਨੀ ਬਣਾਓ ਕਿ ਐਕਸਟਰਿਊਸ਼ਨ ਸਿਲੰਡਰ ਅਤੇ ਉੱਨ ਦੀ ਸਤਹ ਸਾਫ਼ ਅਤੇ ਸੁੱਕੀ ਹੈ;
4. ਇਕਸਾਰ ਗਤੀ ਨੂੰ ਯਕੀਨੀ ਬਣਾਉਣ ਲਈ ਬਾਹਰ ਕੱਢਣ ਦੀ ਗਤੀ ਨੂੰ ਕੰਟਰੋਲ ਕਰੋ.
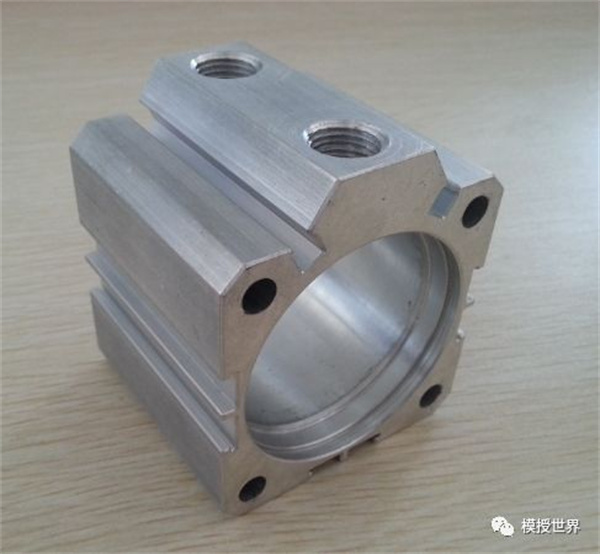
XI.ਉੱਲੀ ਦੇ ਨਿਸ਼ਾਨ
ਇਹ ਬਾਹਰ ਕੱਢੇ ਗਏ ਉਤਪਾਦ ਦੀ ਸਤ੍ਹਾ 'ਤੇ ਲੰਬਕਾਰੀ ਅਸਮਾਨਤਾ ਦਾ ਇੱਕ ਨਿਸ਼ਾਨ ਹੈ, ਅਤੇ ਸਾਰੇ ਬਾਹਰ ਕੱਢੇ ਗਏ ਉਤਪਾਦਾਂ ਦੇ ਵੱਖ-ਵੱਖ ਡਿਗਰੀ ਤੱਕ ਮਰਨ ਦੇ ਚਿੰਨ੍ਹ ਹੁੰਦੇ ਹਨ।
ਉੱਲੀ ਦੇ ਨਿਸ਼ਾਨ ਦਾ ਮੁੱਖ ਕਾਰਨ
ਮੁੱਖ ਕਾਰਨ: ਮੋਲਡ ਵਰਕਿੰਗ ਬੈਲਟ ਪੂਰਨ ਨਿਰਵਿਘਨਤਾ ਪ੍ਰਾਪਤ ਨਹੀਂ ਕਰ ਸਕਦਾ.
ਰੋਕਥਾਮ ਵਿਧੀ
1. ਯਕੀਨੀ ਬਣਾਓ ਕਿ ਮੋਲਡ ਵਰਕਿੰਗ ਬੈਲਟ ਦੀ ਸਤਹ ਸਾਫ਼, ਨਿਰਵਿਘਨ ਅਤੇ ਤਿੱਖੇ ਕਿਨਾਰਿਆਂ ਤੋਂ ਮੁਕਤ ਹੈ;
2. ਉੱਚ ਸਤਹ ਦੀ ਕਠੋਰਤਾ ਨੂੰ ਯਕੀਨੀ ਬਣਾਉਣ ਲਈ ਵਾਜਬ ਨਾਈਟ੍ਰਾਈਡਿੰਗ ਇਲਾਜ;
3. ਉੱਲੀ ਦੀ ਸਹੀ ਮੁਰੰਮਤ ਕਰੋ;
4. ਵਰਕਿੰਗ ਬੈਲਟ ਨੂੰ ਵਾਜਬ ਢੰਗ ਨਾਲ ਡਿਜ਼ਾਈਨ ਕੀਤਾ ਜਾਣਾ ਚਾਹੀਦਾ ਹੈ, ਅਤੇ ਕੰਮ ਕਰਨ ਵਾਲੀ ਬੈਲਟ ਬਹੁਤ ਲੰਬੀ ਨਹੀਂ ਹੋਣੀ ਚਾਹੀਦੀ।
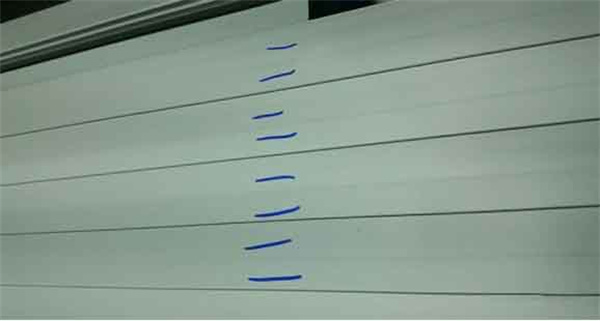
XII.ਮਰੋੜ, ਮੋੜ, ਲਹਿਰ
ਜਿਸ ਵਰਤਾਰੇ ਵਿੱਚ ਐਕਸਟਰੂਡ ਉਤਪਾਦ ਦਾ ਕਰਾਸ ਸੈਕਸ਼ਨ ਕੋਣੀ ਤੌਰ 'ਤੇ ਲੰਬਕਾਰੀ ਦਿਸ਼ਾ ਵਿੱਚ ਡਿਫਲੈਕਟ ਹੁੰਦਾ ਹੈ, ਉਸ ਨੂੰ ਮਰੋੜਨਾ ਕਿਹਾ ਜਾਂਦਾ ਹੈ।ਜਿਸ ਵਰਤਾਰੇ ਵਿੱਚ ਉਤਪਾਦ ਲੰਮੀ ਦਿਸ਼ਾ ਵਿੱਚ ਕਰਵ ਹੁੰਦਾ ਹੈ ਜਾਂ ਚਾਕੂ ਦੀ ਸ਼ਕਲ ਸਿੱਧੀ ਨਹੀਂ ਹੁੰਦੀ ਹੈ ਉਸ ਨੂੰ ਝੁਕਣ ਕਿਹਾ ਜਾਂਦਾ ਹੈ।ਗੁਣਨਫਲ ਦੀ ਲੰਬਕਾਰੀ ਦਿਸ਼ਾ ਵਿੱਚ ਵਾਪਰਨ ਵਾਲੀ ਨਿਰੰਤਰ ਅਨਡੁਲੇਟਿੰਗ ਵਰਤਾਰੇ ਨੂੰ ਤਰੰਗ ਕਿਹਾ ਜਾਂਦਾ ਹੈ।
ਮਰੋੜ, ਝੁਕਣ ਅਤੇ ਲਹਿਰਾਂ ਦੇ ਮੁੱਖ ਕਾਰਨ
1. ਡਾਈ ਹੋਲ ਦਾ ਡਿਜ਼ਾਈਨ ਅਤੇ ਪ੍ਰਬੰਧ ਵਧੀਆ ਨਹੀਂ ਹਨ, ਜਾਂ ਵਰਕਿੰਗ ਬੈਲਟ ਦੇ ਆਕਾਰ ਦੀ ਵੰਡ ਗੈਰ-ਵਾਜਬ ਹੈ;
2. ਡਾਈ ਹੋਲ ਦੀ ਮਾੜੀ ਮਸ਼ੀਨਿੰਗ ਸ਼ੁੱਧਤਾ;
3. ਸਹੀ ਗਾਈਡ ਸਥਾਪਤ ਨਹੀਂ ਹੈ;
4. ਅਣਉਚਿਤ ਉੱਲੀ ਦੀ ਮੁਰੰਮਤ;
5. ਗਲਤ ਐਕਸਟਰਿਊਸ਼ਨ ਤਾਪਮਾਨ ਅਤੇ ਗਤੀ;
6. ਹੱਲ ਦੇ ਇਲਾਜ ਤੋਂ ਪਹਿਲਾਂ ਉਤਪਾਦ ਨੂੰ ਪਹਿਲਾਂ ਤੋਂ ਸਿੱਧਾ ਨਹੀਂ ਕੀਤਾ ਜਾਂਦਾ ਹੈ;
7. ਔਨਲਾਈਨ ਗਰਮੀ ਦੇ ਇਲਾਜ ਦੌਰਾਨ ਅਸਮਾਨ ਕੂਲਿੰਗ.
ਰੋਕਥਾਮ ਵਿਧੀ
1. ਮੋਲਡ ਡਿਜ਼ਾਈਨ ਅਤੇ ਨਿਰਮਾਣ ਦਾ ਉੱਚ ਪੱਧਰ;
2. ਇੱਕ ਢੁਕਵੀਂ ਗਾਈਡ, ਟ੍ਰੈਕਸ਼ਨ ਅਤੇ ਐਕਸਟਰਿਊਸ਼ਨ ਸਥਾਪਿਤ ਕਰੋ;
3. ਸਥਾਨਕ ਲੁਬਰੀਕੇਸ਼ਨ, ਮੋਲਡ ਦੀ ਮੁਰੰਮਤ ਅਤੇ ਡਾਇਵਰਸ਼ਨ ਦੀ ਵਰਤੋਂ ਕਰੋ ਜਾਂ ਧਾਤ ਦੇ ਵਹਾਅ ਦੀ ਦਰ ਨੂੰ ਅਨੁਕੂਲ ਕਰਨ ਲਈ ਸ਼ੰਟ ਹੋਲ ਦੇ ਡਿਜ਼ਾਈਨ ਨੂੰ ਬਦਲੋ;
4. ਵਿਗਾੜ ਨੂੰ ਹੋਰ ਇਕਸਾਰ ਬਣਾਉਣ ਲਈ ਐਕਸਟਰਿਊਸ਼ਨ ਤਾਪਮਾਨ ਅਤੇ ਗਤੀ ਨੂੰ ਵਾਜਬ ਤੌਰ 'ਤੇ ਵਿਵਸਥਿਤ ਕਰੋ;
5. ਘੋਲ ਦੇ ਇਲਾਜ ਦੇ ਤਾਪਮਾਨ ਨੂੰ ਢੁਕਵੇਂ ਢੰਗ ਨਾਲ ਘਟਾਓ ਜਾਂ ਘੋਲ ਦੇ ਇਲਾਜ ਲਈ ਪਾਣੀ ਦਾ ਤਾਪਮਾਨ ਵਧਾਓ;
6. ਔਨਲਾਈਨ ਬੁਝਾਉਣ ਦੇ ਦੌਰਾਨ ਇਕਸਾਰ ਕੂਲਿੰਗ ਨੂੰ ਯਕੀਨੀ ਬਣਾਓ।
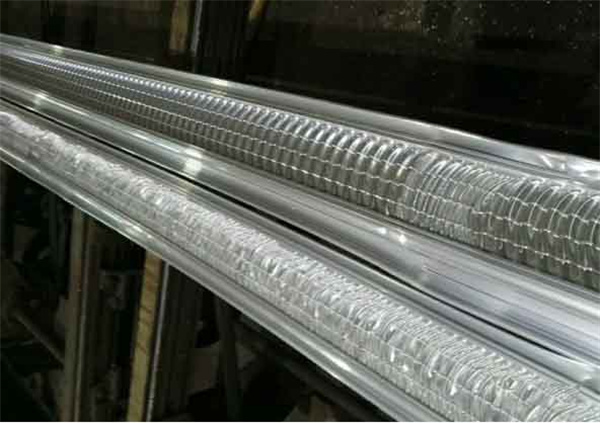
XIII.ਸਖ਼ਤ ਮੋੜ
ਲੰਬਾਈ ਦੀ ਦਿਸ਼ਾ ਵਿੱਚ ਕਿਤੇ ਬਾਹਰ ਕੱਢੇ ਗਏ ਉਤਪਾਦ ਦੇ ਅਚਾਨਕ ਝੁਕਣ ਨੂੰ ਸਖ਼ਤ ਮੋੜ ਕਿਹਾ ਜਾਂਦਾ ਹੈ।
ਸਖ਼ਤ ਝੁਕਣ ਦਾ ਮੁੱਖ ਕਾਰਨ
1. ਅਸਮਾਨ ਐਕਸਟਰਿਊਸ਼ਨ ਸਪੀਡ, ਘੱਟ ਸਪੀਡ ਤੋਂ ਹਾਈ ਸਪੀਡ ਵਿੱਚ ਅਚਾਨਕ ਤਬਦੀਲੀ, ਜਾਂ ਤੇਜ਼ ਰਫ਼ਤਾਰ ਤੋਂ ਘੱਟ ਗਤੀ ਵਿੱਚ ਅਚਾਨਕ ਤਬਦੀਲੀ, ਅਤੇ ਅਚਾਨਕ ਰੁਕਣਾ;
2. ਬਾਹਰ ਕੱਢਣ ਦੀ ਪ੍ਰਕਿਰਿਆ ਦੌਰਾਨ ਉਤਪਾਦ ਨੂੰ ਸਖ਼ਤੀ ਨਾਲ ਹਿਲਾਓ;
3. ਐਕਸਟਰੂਡਰ ਦੀ ਕੰਮ ਕਰਨ ਵਾਲੀ ਸਤਹ ਅਸਮਾਨ ਹੈ.
ਰੋਕਥਾਮ ਵਿਧੀ
1. ਬੇਤਰਤੀਬੇ 'ਤੇ ਨਾ ਰੁਕੋ ਜਾਂ ਅਚਾਨਕ ਬਾਹਰ ਕੱਢਣ ਦੀ ਗਤੀ ਨੂੰ ਨਾ ਬਦਲੋ;
2. ਪ੍ਰੋਫਾਈਲ ਨੂੰ ਅਚਾਨਕ ਹੱਥ ਨਾਲ ਨਾ ਹਿਲਾਓ;
3. ਯਕੀਨੀ ਬਣਾਓ ਕਿ ਡਿਸਚਾਰਜ ਟੇਬਲ ਫਲੈਟ ਹੈ ਅਤੇ ਡਿਸਚਾਰਜ ਰੋਲਰ ਟੇਬਲ ਨਿਰਵਿਘਨ ਹੈ, ਵਿਦੇਸ਼ੀ ਪਦਾਰਥਾਂ ਤੋਂ ਬਿਨਾਂ, ਅਤੇ ਸੰਯੁਕਤ ਉਤਪਾਦ ਬਿਨਾਂ ਰੁਕਾਵਟ ਹੈ।
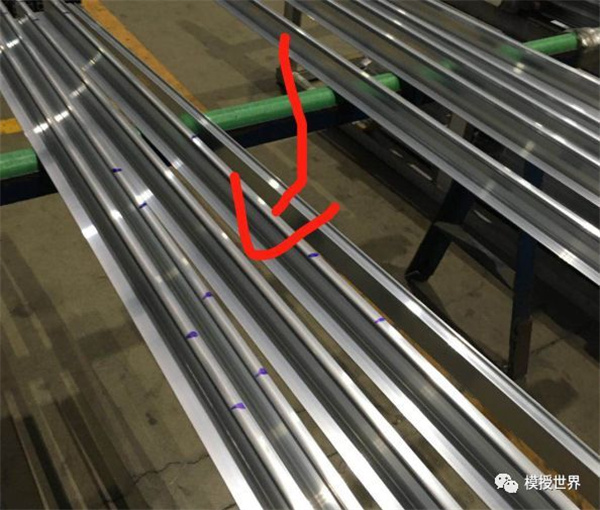
XIV.ਭੰਗ ਨੂਡਲਜ਼
ਇਹ ਐਕਸਟਰੂਡ ਉਤਪਾਦ ਦੀ ਸਤਹ ਦਾ ਨੁਕਸ ਹੈ, ਜਿਸਦਾ ਮਤਲਬ ਹੈ ਕਿ ਉਤਪਾਦ ਦੀ ਸਤਹ ਛੋਟੀ ਅਸਮਾਨਤਾ ਦੇ ਨਾਲ ਲਗਾਤਾਰ ਫਲੇਕਸ, ਸਪਾਟ ਸਕ੍ਰੈਚ, ਟੋਏ, ਮੈਟਲ ਬੀਨਜ਼, ਆਦਿ ਹੈ।
ਪੋਕਮਾਰਕ ਦਾ ਮੁੱਖ ਕਾਰਨ
1. ਉੱਲੀ ਦੀ ਕਠੋਰਤਾ ਕਾਫ਼ੀ ਨਹੀਂ ਹੈ ਜਾਂ ਕਠੋਰਤਾ ਅਸਮਾਨ ਹੈ;
2. ਬਾਹਰ ਕੱਢਣ ਦਾ ਤਾਪਮਾਨ ਬਹੁਤ ਜ਼ਿਆਦਾ ਹੈ;
3. ਬਾਹਰ ਕੱਢਣ ਦੀ ਗਤੀ ਬਹੁਤ ਤੇਜ਼ ਹੈ;
4. ਮੋਲਡ ਦਾ ਕੰਮ ਕਰਨ ਵਾਲਾ ਬੈਲਟ ਬਹੁਤ ਲੰਬਾ, ਮੋਟਾ ਜਾਂ ਧਾਤ ਨਾਲ ਫਸਿਆ ਹੋਇਆ ਹੈ;
5. ਬਾਹਰ ਕੱਢਿਆ ਉੱਨ ਬਹੁਤ ਲੰਬਾ ਹੈ.
ਰੋਕਥਾਮ ਵਿਧੀ
1. ਮੋਲਡ ਵਰਕਿੰਗ ਬੈਲਟ ਦੀ ਕਠੋਰਤਾ ਅਤੇ ਕਠੋਰਤਾ ਦੀ ਇਕਸਾਰਤਾ ਵਿੱਚ ਸੁਧਾਰ ਕਰੋ;
2. ਨਿਯਮਾਂ ਦੇ ਅਨੁਸਾਰ ਐਕਸਟਰਿਊਸ਼ਨ ਸਿਲੰਡਰ ਅਤੇ ਇੰਗੋਟ ਨੂੰ ਗਰਮ ਕਰੋ, ਅਤੇ ਉਚਿਤ ਐਕਸਟਰਿਊਸ਼ਨ ਗਤੀ ਦੀ ਵਰਤੋਂ ਕਰੋ;
3. ਢਾਲ ਨੂੰ ਉਚਿਤ ਢੰਗ ਨਾਲ ਡਿਜ਼ਾਈਨ ਕਰੋ, ਕੰਮ ਕਰਨ ਵਾਲੀ ਪੱਟੀ ਦੀ ਸਤਹ ਦੀ ਖੁਰਦਰੀ ਨੂੰ ਘਟਾਓ, ਅਤੇ ਸਤਹ ਦੇ ਨਿਰੀਖਣ, ਮੁਰੰਮਤ ਅਤੇ ਪਾਲਿਸ਼ਿੰਗ ਨੂੰ ਮਜ਼ਬੂਤ ਕਰੋ;
4. ਇੱਕ ਵਾਜਬ ਇੰਗਟ ਲੰਬਾਈ ਦੀ ਵਰਤੋਂ ਕਰੋ।
XV.ਧਾਤੂ ਦਬਾਉਣ
ਬਾਹਰ ਕੱਢਣ ਦੀ ਪ੍ਰਕਿਰਿਆ ਦੇ ਦੌਰਾਨ, ਮੈਟਲ ਚਿਪਸ ਨੂੰ ਉਤਪਾਦ ਦੀ ਸਤਹ ਵਿੱਚ ਦਬਾਇਆ ਜਾਂਦਾ ਹੈ, ਜਿਸਨੂੰ ਮੈਟਲ ਪ੍ਰੈੱਸਿੰਗ ਕਿਹਾ ਜਾਂਦਾ ਹੈ।
ਧਾਤ ਦੇ ਘੁਸਪੈਠ ਦੇ ਮੁੱਖ ਕਾਰਨ:
1. ਉੱਨ ਦੇ ਸਿਰੇ ਨੁਕਸਦਾਰ ਹਨ;
2. ਉੱਨ ਦੀ ਅੰਦਰਲੀ ਸਤਹ ਧਾਤ ਨਾਲ ਫਸ ਗਈ ਹੈ ਜਾਂ ਲੁਬਰੀਕੇਟਿੰਗ ਤੇਲ ਵਿੱਚ ਧਾਤ ਦਾ ਮਲਬਾ ਅਤੇ ਹੋਰ ਗੰਦਗੀ ਸ਼ਾਮਲ ਹੈ;
3. ਬਾਹਰ ਕੱਢਣ ਵਾਲਾ ਸਿਲੰਡਰ ਸਾਫ਼ ਨਹੀਂ ਕੀਤਾ ਗਿਆ ਹੈ, ਅਤੇ ਹੋਰ ਧਾਤ ਦੇ ਮਲਬੇ ਹਨ;
4. ਪਿੰਜੀ ਨੂੰ ਹੋਰ ਧਾਤ ਦੀਆਂ ਵਿਦੇਸ਼ੀ ਵਸਤੂਆਂ ਵਿੱਚ ਡੁਬੋਇਆ ਜਾਂਦਾ ਹੈ;
5. ਉੱਨ ਵਿੱਚ ਸਲੈਗ ਸ਼ਾਮਲ ਹੈ.
ਰੋਕਥਾਮ ਵਿਧੀ
1. ਉੱਨ 'ਤੇ burrs ਹਟਾਓ;
2. ਯਕੀਨੀ ਬਣਾਓ ਕਿ ਉੱਨ ਦੀ ਸਤ੍ਹਾ ਅਤੇ ਲੁਬਰੀਕੇਟਿੰਗ ਤੇਲ ਸਾਫ਼ ਅਤੇ ਸੁੱਕੇ ਹਨ;
3. ਉੱਲੀ ਅਤੇ ਬਾਹਰ ਕੱਢਣ ਵਾਲੇ ਸਿਲੰਡਰ ਵਿੱਚ ਧਾਤ ਦੇ ਮਲਬੇ ਨੂੰ ਸਾਫ਼ ਕਰੋ;
4. ਉੱਚ-ਗੁਣਵੱਤਾ ਵਾਲੀ ਉੱਨ ਦੀ ਚੋਣ ਕਰੋ।
XVI.ਗੈਰ-ਧਾਤੂ ਦਬਾਉਣ
ਬਾਹਰੀ ਪਦਾਰਥ ਜਿਵੇਂ ਕਿ ਪੱਥਰ ਦੇ ਕਾਲੇ ਨੂੰ ਬਾਹਰ ਕੱਢੇ ਗਏ ਉਤਪਾਦ ਦੀਆਂ ਅੰਦਰੂਨੀ ਅਤੇ ਬਾਹਰਲੀਆਂ ਸਤਹਾਂ ਵਿੱਚ ਦਬਾਇਆ ਜਾਂਦਾ ਹੈ, ਜਿਸ ਨੂੰ ਗੈਰ-ਧਾਤੂ ਇੰਡੈਂਟੇਸ਼ਨ ਕਿਹਾ ਜਾਂਦਾ ਹੈ।ਵਿਦੇਸ਼ੀ ਪਦਾਰਥ ਨੂੰ ਸਕ੍ਰੈਪ ਕਰਨ ਤੋਂ ਬਾਅਦ, ਉਤਪਾਦ ਦੀ ਅੰਦਰਲੀ ਸਤਹ ਵੱਖ-ਵੱਖ ਆਕਾਰਾਂ ਦੇ ਦਬਾਅ ਦਿਖਾਏਗੀ, ਜੋ ਉਤਪਾਦ ਦੀ ਸਤਹ ਦੀ ਨਿਰੰਤਰਤਾ ਨੂੰ ਨਸ਼ਟ ਕਰ ਦੇਵੇਗੀ।
ਗੈਰ-ਧਾਤੂ ਘੁਸਪੈਠ ਦਾ ਮੁੱਖ ਕਾਰਨ
1. ਗ੍ਰਾਫਾਈਟ ਕਣ ਦਾ ਆਕਾਰ ਮੋਟਾ ਜਾਂ ਇਕੱਠਾ ਹੁੰਦਾ ਹੈ, ਜਿਸ ਵਿੱਚ ਨਮੀ ਜਾਂ ਤੇਲ ਹੁੰਦਾ ਹੈ, ਅਤੇ ਹਿਲਾਉਣਾ ਅਸਮਾਨ ਹੁੰਦਾ ਹੈ;
2. ਸਿਲੰਡਰ ਤੇਲ ਦਾ ਫਲੈਸ਼ ਪੁਆਇੰਟ ਘੱਟ ਹੈ;
3. ਸਿਲੰਡਰ ਤੇਲ ਅਤੇ ਗ੍ਰੇਫਾਈਟ ਦਾ ਅਨੁਪਾਤ ਗਲਤ ਹੈ, ਅਤੇ ਬਹੁਤ ਜ਼ਿਆਦਾ ਗ੍ਰੇਫਾਈਟ ਹੈ।
ਰੋਕਥਾਮ ਵਿਧੀ
1. ਯੋਗ ਗ੍ਰੈਫਾਈਟ ਦੀ ਵਰਤੋਂ ਕਰੋ ਅਤੇ ਇਸਨੂੰ ਸੁੱਕਾ ਰੱਖੋ;
2. ਫਿਲਟਰ ਕਰੋ ਅਤੇ ਯੋਗ ਲੁਬਰੀਕੇਟਿੰਗ ਤੇਲ ਦੀ ਵਰਤੋਂ ਕਰੋ;
3. ਲੁਬਰੀਕੇਟਿੰਗ ਤੇਲ ਅਤੇ ਗ੍ਰੈਫਾਈਟ ਦੇ ਅਨੁਪਾਤ ਨੂੰ ਨਿਯੰਤਰਿਤ ਕਰੋ।
XVII.ਸਤਹ ਖੋਰ
ਬਾਹਰਲੇ ਉਤਪਾਦ ਜਿਨ੍ਹਾਂ ਦੀ ਸਤਹ ਦਾ ਇਲਾਜ ਨਹੀਂ ਹੋਇਆ ਹੈ, ਬਾਹਰੀ ਮਾਧਿਅਮ ਨਾਲ ਰਸਾਇਣਕ ਜਾਂ ਇਲੈਕਟ੍ਰੋਕੈਮੀਕਲ ਪ੍ਰਤੀਕ੍ਰਿਆ ਤੋਂ ਬਾਅਦ, ਬਾਹਰੀ ਉਤਪਾਦ ਦੀ ਸਤਹ, ਸਤਹ ਦੇ ਸਥਾਨਕ ਨੁਕਸਾਨ ਦੇ ਕਾਰਨ ਨੁਕਸ ਪੈਦਾ ਕਰਦੀ ਹੈ, ਜਿਸ ਨੂੰ ਸਤਹ ਖੋਰ ਕਿਹਾ ਜਾਂਦਾ ਹੈ।ਖੰਡਿਤ ਉਤਪਾਦ ਦੀ ਸਤ੍ਹਾ ਆਪਣੀ ਧਾਤੂ ਚਮਕ ਗੁਆ ਦਿੰਦੀ ਹੈ, ਅਤੇ ਗੰਭੀਰ ਮਾਮਲਿਆਂ ਵਿੱਚ, ਸਤ੍ਹਾ 'ਤੇ ਸਲੇਟੀ-ਚਿੱਟੇ ਖੋਰ ਉਤਪਾਦ ਪੈਦਾ ਹੁੰਦੇ ਹਨ।
ਸਤਹ ਦੇ ਖੋਰ ਦਾ ਮੁੱਖ ਕਾਰਨ
1. ਉਤਪਾਦ ਨੂੰ ਉਤਪਾਦਨ, ਸਟੋਰੇਜ ਅਤੇ ਆਵਾਜਾਈ ਦੇ ਦੌਰਾਨ ਪਾਣੀ, ਐਸਿਡ, ਖਾਰੀ, ਲੂਣ, ਆਦਿ ਵਰਗੇ ਖਰਾਬ ਮਾਧਿਅਮਾਂ ਦੇ ਸੰਪਰਕ ਵਿੱਚ ਆਉਂਦਾ ਹੈ, ਜਾਂ ਲੰਬੇ ਸਮੇਂ ਲਈ ਨਮੀ ਵਾਲੇ ਮਾਹੌਲ ਵਿੱਚ ਪਾਰਕ ਕੀਤਾ ਜਾਂਦਾ ਹੈ;
2. ਗਲਤ ਮਿਸ਼ਰਤ ਰਚਨਾ ਅਨੁਪਾਤ;
ਰੋਕਥਾਮ ਵਿਧੀ
1. ਉਤਪਾਦ ਦੀ ਸਤਹ ਅਤੇ ਉਤਪਾਦਨ ਅਤੇ ਸਟੋਰੇਜ ਵਾਤਾਵਰਨ ਨੂੰ ਸਾਫ਼ ਅਤੇ ਸੁੱਕਾ ਰੱਖੋ;
2. ਮਿਸ਼ਰਤ ਵਿੱਚ ਤੱਤਾਂ ਦੀ ਸਮੱਗਰੀ ਨੂੰ ਨਿਯੰਤਰਿਤ ਕਰੋ।
XVIII.ਸੰਤਰੇ ਦਾ ਛਿਲਕਾ
ਬਾਹਰ ਕੱਢੇ ਗਏ ਉਤਪਾਦ ਦੀ ਸਤ੍ਹਾ 'ਤੇ ਸੰਤਰੇ ਦੇ ਛਿਲਕੇ ਵਰਗੀਆਂ ਅਸਮਾਨ ਝੁਰੜੀਆਂ ਹੁੰਦੀਆਂ ਹਨ, ਜਿਨ੍ਹਾਂ ਨੂੰ ਸਤਹ ਦੀਆਂ ਝੁਰੜੀਆਂ ਵੀ ਕਿਹਾ ਜਾਂਦਾ ਹੈ।ਇਹ ਬਾਹਰ ਕੱਢਣ ਦੌਰਾਨ ਮੋਟੇ ਦਾਣਿਆਂ ਕਾਰਨ ਹੁੰਦਾ ਹੈ।ਜਿੰਨੇ ਮੋਟੇ ਦਾਣੇ ਹੋਣਗੇ, ਝੁਰੜੀਆਂ ਓਨੀਆਂ ਹੀ ਸਪੱਸ਼ਟ ਹਨ।
ਸੰਤਰੇ ਦੇ ਛਿਲਕੇ ਦਾ ਮੁੱਖ ਕਾਰਨ
1. ਪਿੰਜਰ ਦਾ ਢਾਂਚਾ ਅਸਮਾਨ ਹੈ ਅਤੇ ਸਮਰੂਪਤਾ ਦਾ ਇਲਾਜ ਨਾਕਾਫ਼ੀ ਹੈ;
2. ਬਾਹਰ ਕੱਢਣ ਦੀਆਂ ਸਥਿਤੀਆਂ ਗੈਰ-ਵਾਜਬ ਹਨ, ਅਤੇ ਤਿਆਰ ਉਤਪਾਦਾਂ ਦੇ ਅਨਾਜ ਮੋਟੇ ਹਨ;
3. ਖਿੱਚਣ ਅਤੇ ਸਿੱਧਾ ਕਰਨ ਦੀ ਮਾਤਰਾ ਬਹੁਤ ਜ਼ਿਆਦਾ ਹੈ.
ਰੋਕਥਾਮ ਵਿਧੀ
1. ਸਮਰੂਪੀਕਰਨ ਪ੍ਰਕਿਰਿਆ ਨੂੰ ਉਚਿਤ ਢੰਗ ਨਾਲ ਨਿਯੰਤਰਿਤ ਕਰੋ;
2. ਵਿਗਾੜ ਜਿੰਨਾ ਸੰਭਵ ਹੋ ਸਕੇ ਇਕਸਾਰ ਹੋਣਾ ਚਾਹੀਦਾ ਹੈ (ਐਕਸਟਰਿਊਸ਼ਨ ਤਾਪਮਾਨ, ਗਤੀ, ਆਦਿ ਨੂੰ ਨਿਯੰਤਰਿਤ ਕਰੋ)
3. ਤਣਾਅ ਸੁਧਾਰ ਦੀ ਮਾਤਰਾ ਨੂੰ ਬਹੁਤ ਜ਼ਿਆਦਾ ਨਾ ਹੋਣ ਲਈ ਕੰਟਰੋਲ ਕਰੋ।
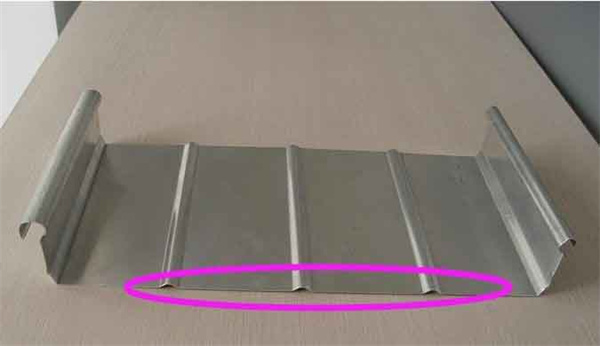
XIX.ਅਸਮਾਨ
ਐਕਸਟਰਿਊਸ਼ਨ ਤੋਂ ਬਾਅਦ, ਉਹ ਖੇਤਰ ਜਿੱਥੇ ਉਤਪਾਦ ਦੀ ਮੋਟਾਈ ਸਮਤਲ 'ਤੇ ਬਦਲਦੀ ਹੈ, ਉਹ ਕੋਨਵੇਕਸ ਜਾਂ ਕਨਵੈਕਸ ਦਿਖਾਈ ਦਿੰਦਾ ਹੈ।ਆਮ ਤੌਰ 'ਤੇ, ਇਸ ਨੂੰ ਨੰਗੀ ਅੱਖ ਨਾਲ ਦੇਖਿਆ ਨਹੀਂ ਜਾ ਸਕਦਾ ਹੈ।ਸਤ੍ਹਾ ਦੇ ਇਲਾਜ ਤੋਂ ਬਾਅਦ, ਵਧੀਆ ਪਰਛਾਵੇਂ ਜਾਂ ਹੱਡੀਆਂ ਦੇ ਪਰਛਾਵੇਂ ਦਿਖਾਈ ਦਿੰਦੇ ਹਨ।
ਅਸਮਾਨਤਾ ਦਾ ਮੁੱਖ ਕਾਰਨ
1. ਮੋਲਡ ਵਰਕਿੰਗ ਬੈਲਟ ਸਹੀ ਢੰਗ ਨਾਲ ਡਿਜ਼ਾਈਨ ਨਹੀਂ ਕੀਤੀ ਗਈ ਹੈ, ਅਤੇ ਉੱਲੀ ਦੀ ਮੁਰੰਮਤ ਜਗ੍ਹਾ 'ਤੇ ਨਹੀਂ ਹੈ;
2. ਸ਼ੰਟ ਹੋਲ ਜਾਂ ਪ੍ਰੀ-ਚੈਂਬਰ ਦਾ ਆਕਾਰ ਢੁਕਵਾਂ ਨਹੀਂ ਹੈ, ਅਤੇ ਕਰਾਸ ਖੇਤਰ ਵਿੱਚ ਪ੍ਰੋਫਾਈਲ ਨੂੰ ਖਿੱਚਣ ਜਾਂ ਫੈਲਾਉਣ ਦੀ ਤਾਕਤ ਜਹਾਜ਼ ਵਿੱਚ ਮਾਮੂਲੀ ਤਬਦੀਲੀ ਦਾ ਕਾਰਨ ਬਣਦੀ ਹੈ;
3. ਕੂਲਿੰਗ ਪ੍ਰਕਿਰਿਆ ਅਸਮਾਨ ਹੁੰਦੀ ਹੈ, ਅਤੇ ਮੋਟੀ-ਦੀਵਾਰ ਵਾਲੇ ਹਿੱਸੇ ਜਾਂ ਇਕ ਦੂਜੇ ਨੂੰ ਕੱਟਣ ਵਾਲੇ ਹਿੱਸੇ ਦੀ ਕੂਲਿੰਗ ਦੀ ਗਤੀ ਹੌਲੀ ਹੁੰਦੀ ਹੈ, ਜਿਸ ਦੇ ਨਤੀਜੇ ਵਜੋਂ ਕੂਲਿੰਗ ਪ੍ਰਕਿਰਿਆ ਦੌਰਾਨ ਜਹਾਜ਼ ਦੇ ਸੁੰਗੜਨ ਅਤੇ ਵਿਗਾੜ ਦੀਆਂ ਵੱਖ-ਵੱਖ ਡਿਗਰੀਆਂ ਹੁੰਦੀਆਂ ਹਨ;
4. ਮੋਟਾਈ ਵਿੱਚ ਵੱਡੇ ਅੰਤਰ ਦੇ ਕਾਰਨ, ਮੋਟੀ-ਦੀਵਾਰ ਵਾਲੇ ਹਿੱਸੇ ਜਾਂ ਪਰਿਵਰਤਨ ਖੇਤਰ ਦੇ ਸੰਗਠਨ ਅਤੇ ਸੰਗਠਨ ਦੇ ਹੋਰ ਹਿੱਸਿਆਂ ਵਿੱਚ ਅੰਤਰ ਵਧਦਾ ਹੈ।
ਰੋਕਥਾਮ ਵਿਧੀ
1. ਉੱਲੀ ਦੇ ਡਿਜ਼ਾਈਨ, ਨਿਰਮਾਣ ਅਤੇ ਉੱਲੀ ਦੀ ਮੁਰੰਮਤ ਦੇ ਪੱਧਰ ਨੂੰ ਸੁਧਾਰੋ;
2. ਇਕਸਾਰ ਕੂਲਿੰਗ ਗਤੀ ਨੂੰ ਯਕੀਨੀ ਬਣਾਓ।
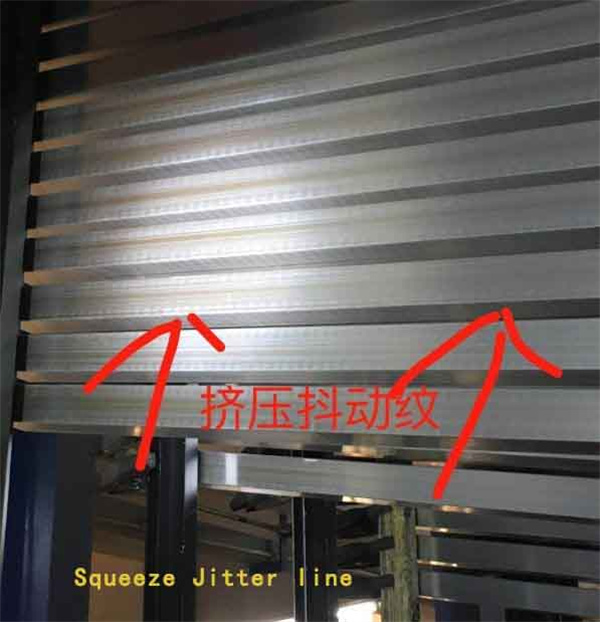
ਐਕਸ.ਐਕਸ.ਵਾਈਬ੍ਰੇਸ਼ਨ ਪੈਟਰਨ
ਇਹ ਐਕਸਟਰੂਡ ਉਤਪਾਦ ਦੀ ਸਤ੍ਹਾ ਤੱਕ ਇੱਕ ਆਵਰਤੀ ਸਟ੍ਰੀਕ ਨੁਕਸ ਟ੍ਰਾਂਸਵਰਸ ਹੈ।ਇਹ ਉਤਪਾਦ ਦੀ ਸਤ੍ਹਾ 'ਤੇ ਹਰੀਜੱਟਲ ਨਿਰੰਤਰ ਸਮੇਂ-ਸਮੇਂ ਦੀਆਂ ਧਾਰੀਆਂ ਦੁਆਰਾ ਦਰਸਾਇਆ ਜਾਂਦਾ ਹੈ, ਅਤੇ ਸਟ੍ਰਿਪ ਕਰਵ ਮੋਲਡ ਦੀ ਕਾਰਜਸ਼ੀਲ ਪੱਟੀ ਦੀ ਸ਼ਕਲ ਦੇ ਨਾਲ ਇਕਸਾਰ ਹੁੰਦਾ ਹੈ, ਅਤੇ ਗੰਭੀਰ ਮਾਮਲਿਆਂ ਵਿੱਚ, ਇੱਕ ਸਪੱਸ਼ਟ ਉਛਾਲ ਮਹਿਸੂਸ ਹੁੰਦਾ ਹੈ।
ਵਾਈਬ੍ਰੇਸ਼ਨ ਦਾ ਮੁੱਖ ਕਾਰਨ
1. ਐਕਸਟਰਿਊਸ਼ਨ ਸ਼ਾਫਟ ਸਾਜ਼ੋ-ਸਾਮਾਨ ਦੇ ਕਾਰਨਾਂ ਕਰਕੇ ਅੱਗੇ ਵਧਦਾ ਹੈ ਅਤੇ ਹਿੱਲਦਾ ਹੈ, ਜਿਸ ਨਾਲ ਧਾਤ ਦੇ ਹਿੱਲਣ ਦਾ ਕਾਰਨ ਬਣਦਾ ਹੈ ਜਦੋਂ ਇਹ ਮੋਰੀ ਤੋਂ ਬਾਹਰ ਨਿਕਲਦਾ ਹੈ;
2. ਧਾਤ ਹਿੱਲਦੀ ਹੈ ਜਦੋਂ ਇਹ ਉੱਲੀ ਦੇ ਕਾਰਨ ਡਾਈ ਹੋਲ ਤੋਂ ਬਾਹਰ ਵਹਿ ਜਾਂਦੀ ਹੈ;
3. ਮੋਲਡ ਸਪੋਰਟ ਪੈਡ ਢੁਕਵਾਂ ਨਹੀਂ ਹੈ, ਮੋਲਡ ਦੀ ਕਠੋਰਤਾ ਚੰਗੀ ਨਹੀਂ ਹੈ, ਅਤੇ ਵਾਈਬ੍ਰੇਸ਼ਨ ਉਦੋਂ ਹੁੰਦੀ ਹੈ ਜਦੋਂ ਐਕਸਟਰਿਊਸ਼ਨ ਫੋਰਸ ਉਤਰਾਅ-ਚੜ੍ਹਾਅ ਹੁੰਦੀ ਹੈ।
ਰੋਕਥਾਮ ਵਿਧੀ
1. ਯੋਗ ਮੋਲਡਾਂ ਦੀ ਵਰਤੋਂ ਕਰੋ;
2. ਢੁਕਵੇਂ ਸਮਰਥਨ ਪੈਡਾਂ ਦੀ ਵਰਤੋਂ ਕੀਤੀ ਜਾਣੀ ਚਾਹੀਦੀ ਹੈ ਜਦੋਂ ਉੱਲੀ ਸਥਾਪਿਤ ਕੀਤੀ ਜਾਂਦੀ ਹੈ;
3. ਸਾਜ਼-ਸਾਮਾਨ ਨੂੰ ਅਡਜੱਸਟ ਕਰੋ.
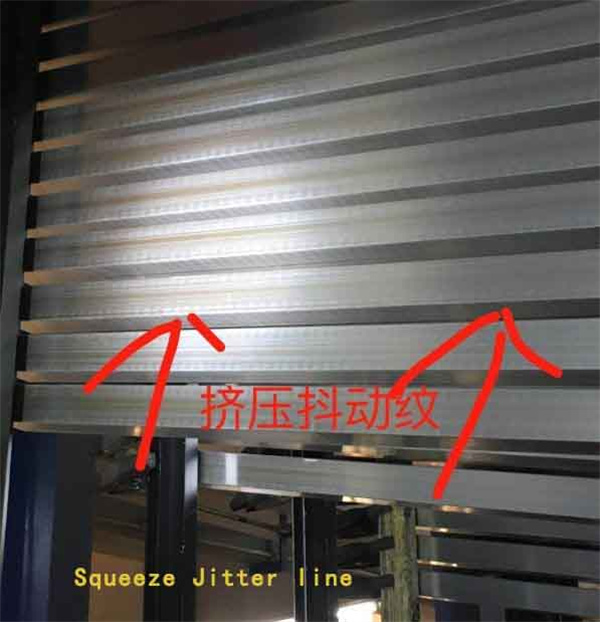
XXI, ਮਿਸ਼ਰਤ
ਸ਼ਾਮਲ ਹੋਣ ਦਾ ਮੁੱਖ ਕਾਰਨ
ਕਿਉਂਕਿ ਸੰਮਿਲਨ ਬਿਲਟ ਵਿੱਚ ਧਾਤ ਜਾਂ ਗੈਰ-ਧਾਤੂ ਸੰਮਿਲਨ ਹਨ, ਇਹ ਪਿਛਲੀ ਪ੍ਰਕਿਰਿਆ ਵਿੱਚ ਨਹੀਂ ਪਾਇਆ ਗਿਆ ਸੀ, ਅਤੇ ਐਕਸਟਰਿਊਸ਼ਨ ਤੋਂ ਬਾਅਦ ਉਤਪਾਦ ਦੀ ਸਤਹ ਜਾਂ ਅੰਦਰ ਰਿਹਾ।
ਰੋਕਥਾਮ ਵਿਧੀ
ਧਾਤ ਜਾਂ ਗੈਰ-ਧਾਤੂ ਸੰਮਿਲਨਾਂ ਨੂੰ ਬਾਹਰ ਕੱਢਣ ਦੀ ਪ੍ਰਕਿਰਿਆ ਵਿੱਚ ਦਾਖਲ ਹੋਣ ਤੋਂ ਰੋਕਣ ਲਈ ਬਿਲਟ (ਅਲਟਰਾਸੋਨਿਕ ਨਿਰੀਖਣ ਸਮੇਤ) ਦੇ ਨਿਰੀਖਣ ਨੂੰ ਮਜ਼ਬੂਤ ਕਰੋ।

XXII, ਪਾਣੀ ਦੇ ਚਿੰਨ੍ਹ
ਉਤਪਾਦ ਦੀ ਸਤ੍ਹਾ 'ਤੇ ਹਲਕੇ ਚਿੱਟੇ ਜਾਂ ਹਲਕੇ ਕਾਲੇ ਅਨਿਯਮਿਤ ਵਾਟਰਲਾਈਨ ਦੇ ਚਿੰਨ੍ਹ ਨੂੰ ਪਾਣੀ ਦੇ ਚਿੰਨ੍ਹ ਕਿਹਾ ਜਾਂਦਾ ਹੈ।
ਪਾਣੀ ਦੇ ਨਿਸ਼ਾਨ ਦਾ ਮੁੱਖ ਕਾਰਨ
1. ਸਫਾਈ ਦੇ ਬਾਅਦ ਸੁਕਾਉਣਾ ਚੰਗਾ ਨਹੀਂ ਹੈ, ਅਤੇ ਉਤਪਾਦ ਦੀ ਸਤਹ 'ਤੇ ਬਕਾਇਆ ਨਮੀ ਹੈ;
2. ਬਾਰਿਸ਼ ਅਤੇ ਹੋਰ ਕਾਰਨਾਂ ਕਰਕੇ ਉਤਪਾਦ ਦੀ ਸਤ੍ਹਾ 'ਤੇ ਬਚੀ ਨਮੀ ਨੂੰ ਸਮੇਂ ਸਿਰ ਸਾਫ਼ ਨਹੀਂ ਕੀਤਾ ਗਿਆ ਹੈ;
3. ਬੁਢਾਪੇ ਦੇ ਭੱਠੀ ਦੇ ਬਾਲਣ ਵਿੱਚ ਪਾਣੀ ਹੁੰਦਾ ਹੈ, ਅਤੇ ਬੁਢਾਪੇ ਦੇ ਬਾਅਦ ਉਤਪਾਦ ਦੇ ਠੰਢੇ ਹੋਣ ਦੇ ਦੌਰਾਨ ਉਤਪਾਦ ਦੀ ਸਤਹ 'ਤੇ ਪਾਣੀ ਸੰਘਣਾ ਹੁੰਦਾ ਹੈ;
4. ਬੁਢਾਪੇ ਵਾਲੀ ਭੱਠੀ ਦਾ ਬਾਲਣ ਸਾਫ਼ ਨਹੀਂ ਹੈ, ਅਤੇ ਉਤਪਾਦ ਦੀ ਸਤਹ ਬਲਨ ਤੋਂ ਬਾਅਦ ਸਲਫਰ ਡਾਈਆਕਸਾਈਡ ਦੁਆਰਾ ਖਰਾਬ ਹੋ ਜਾਂਦੀ ਹੈ ਜਾਂ ਧੂੜ ਦੁਆਰਾ ਪ੍ਰਦੂਸ਼ਿਤ ਹੁੰਦੀ ਹੈ;
5. ਬੁਝਾਉਣ ਵਾਲਾ ਮਾਧਿਅਮ ਪ੍ਰਦੂਸ਼ਿਤ ਹੈ।
ਰੋਕਥਾਮ ਵਿਧੀ
1. ਉਤਪਾਦ ਦੀ ਸਤ੍ਹਾ ਨੂੰ ਸੁੱਕਾ ਅਤੇ ਸਾਫ਼ ਰੱਖੋ;
2. ਨਮੀ ਦੀ ਸਮਗਰੀ ਅਤੇ ਬੁਢਾਪੇ ਦੇ ਚਾਰਜ ਦੀ ਸਫਾਈ ਨੂੰ ਨਿਯੰਤਰਿਤ ਕਰੋ;
3. ਬੁਝਾਉਣ ਵਾਲੇ ਮਾਧਿਅਮ ਦੇ ਪ੍ਰਬੰਧਨ ਨੂੰ ਮਜ਼ਬੂਤ ਕਰੋ।
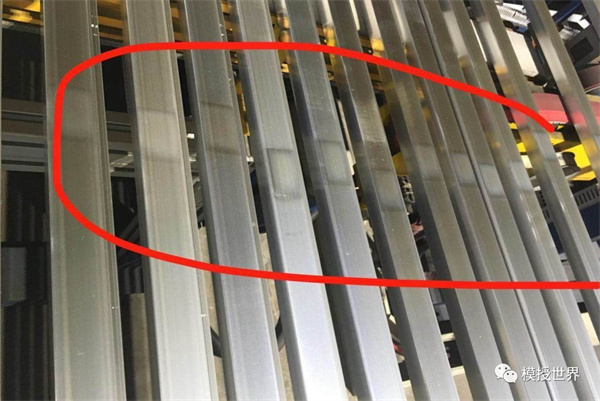
XXIII.ਪਾੜਾ
ਰੂਲਰ ਨੂੰ ਬਾਹਰ ਕੱਢੇ ਗਏ ਉਤਪਾਦ ਦੇ ਇੱਕ ਨਿਸ਼ਚਿਤ ਪਲੇਨ ਉੱਤੇ ਖਿਤਿਜੀ ਰੂਪ ਵਿੱਚ ਉੱਚਿਤ ਕੀਤਾ ਜਾਂਦਾ ਹੈ, ਅਤੇ ਸ਼ਾਸਕ ਅਤੇ ਸਤਹ ਦੇ ਵਿਚਕਾਰ ਇੱਕ ਖਾਸ ਪਾੜਾ ਹੁੰਦਾ ਹੈ, ਜਿਸਨੂੰ ਇੱਕ ਪਾੜਾ ਕਿਹਾ ਜਾਂਦਾ ਹੈ।
ਪਾੜੇ ਦਾ ਮੁੱਖ ਕਾਰਨ
ਐਕਸਟਰਿਊਸ਼ਨ ਜਾਂ ਗਲਤ ਫਿਨਿਸ਼ਿੰਗ ਅਤੇ ਸਿੱਧਾ ਕਰਨ ਦੇ ਕਾਰਜਾਂ ਦੌਰਾਨ ਅਸਮਾਨ ਧਾਤ ਦਾ ਪ੍ਰਵਾਹ।
ਰੋਕਥਾਮ ਵਿਧੀ
ਢਾਂਚਿਆਂ ਨੂੰ ਢੁਕਵੇਂ ਢੰਗ ਨਾਲ ਡਿਜ਼ਾਈਨ ਕਰੋ ਅਤੇ ਨਿਰਮਾਣ ਕਰੋ, ਮੋਲਡ ਦੀ ਮੁਰੰਮਤ ਨੂੰ ਮਜ਼ਬੂਤ ਕਰੋ, ਅਤੇ ਨਿਯਮਾਂ ਦੇ ਅਨੁਸਾਰ ਸਖਤੀ ਨਾਲ ਐਕਸਟਰਿਊਸ਼ਨ ਤਾਪਮਾਨ ਅਤੇ ਐਕਸਟਰਿਊਸ਼ਨ ਗਤੀ ਨੂੰ ਕੰਟਰੋਲ ਕਰੋ।
XXIV, ਅਸਮਾਨ ਕੰਧ ਮੋਟਾਈ
ਇੱਕੋ ਆਕਾਰ ਦੇ ਬਾਹਰ ਕੱਢੇ ਗਏ ਉਤਪਾਦਾਂ ਵਿੱਚ ਇੱਕੋ ਭਾਗ ਜਾਂ ਲੰਬਕਾਰੀ ਦਿਸ਼ਾ ਵਿੱਚ ਪਤਲੀਆਂ ਜਾਂ ਮੋਟੀਆਂ ਕੰਧਾਂ ਹੁੰਦੀਆਂ ਹਨ, ਅਤੇ ਇਸ ਵਰਤਾਰੇ ਨੂੰ ਅਸਮਾਨ ਕੰਧ ਮੋਟਾਈ ਕਿਹਾ ਜਾਂਦਾ ਹੈ।
ਅਸਮਾਨ ਕੰਧ ਮੋਟਾਈ ਦਾ ਮੁੱਖ ਕਾਰਨ
1. ਮੋਲਡ ਡਿਜ਼ਾਈਨ ਗੈਰ-ਵਾਜਬ ਹੈ, ਜਾਂ ਟੂਲ ਅਤੇ ਮੋਲਡ ਅਸੈਂਬਲੀ ਗਲਤ ਹੈ;
2. ਐਕਸਟਰੂਜ਼ਨ ਸਿਲੰਡਰ ਅਤੇ ਐਕਸਟਰੂਜ਼ਨ ਸੂਈ ਇੱਕੋ ਸੈਂਟਰਲਾਈਨ 'ਤੇ ਨਹੀਂ ਹਨ, ਜੋ ਕਿ ਇਕਸੈਂਟ੍ਰਿਕਿਟੀ ਬਣਾਉਂਦੇ ਹਨ;
3. ਐਕਸਟਰਿਊਸ਼ਨ ਸਿਲੰਡਰ ਦੀ ਲਾਈਨਿੰਗ ਬਹੁਤ ਜ਼ਿਆਦਾ ਪਹਿਨੀ ਜਾਂਦੀ ਹੈ, ਅਤੇ ਉੱਲੀ ਨੂੰ ਮਜ਼ਬੂਤੀ ਨਾਲ ਸਥਿਰ ਨਹੀਂ ਕੀਤਾ ਜਾ ਸਕਦਾ, ਨਤੀਜੇ ਵਜੋਂ ਸਨਕੀਤਾ ਹੁੰਦੀ ਹੈ;
4. ਪਹਿਲੇ ਅਤੇ ਦੂਜੇ ਐਕਸਟਰਿਊਸ਼ਨ ਤੋਂ ਬਾਅਦ ਇੰਗੌਟ ਖਾਲੀ ਦੀ ਅਸਮਾਨ ਕੰਧ ਮੋਟਾਈ ਆਪਣੇ ਆਪ ਨੂੰ ਖਤਮ ਨਹੀਂ ਕੀਤਾ ਜਾ ਸਕਦਾ ਹੈ।ਬਾਹਰ ਕੱਢਣ ਤੋਂ ਬਾਅਦ ਉੱਨ ਦੀ ਅਸਮਾਨ ਕੰਧ ਮੋਟਾਈ ਨੂੰ ਰੋਲਿੰਗ ਅਤੇ ਖਿੱਚਣ ਤੋਂ ਬਾਅਦ ਹਟਾਇਆ ਨਹੀਂ ਜਾਂਦਾ;
5. ਲੁਬਰੀਕੇਟਿੰਗ ਤੇਲ ਅਸਮਾਨਤਾ ਨਾਲ ਲਗਾਇਆ ਜਾਂਦਾ ਹੈ, ਜਿਸ ਨਾਲ ਧਾਤ ਦਾ ਵਹਾਅ ਅਸਮਾਨ ਹੁੰਦਾ ਹੈ।
ਰੋਕਥਾਮ ਵਿਧੀ
1. ਟੂਲਿੰਗ ਅਤੇ ਮੋਲਡ ਦੇ ਡਿਜ਼ਾਈਨ ਅਤੇ ਨਿਰਮਾਣ ਨੂੰ ਅਨੁਕੂਲ ਬਣਾਓ, ਅਤੇ ਤਰਕਸੰਗਤ ਤੌਰ 'ਤੇ ਇਕੱਠੇ ਕਰੋ ਅਤੇ ਅਨੁਕੂਲ ਬਣਾਓ;
2. ਐਕਸਟਰੂਡਰ ਅਤੇ ਐਕਸਟਰੂਜ਼ਨ ਡਾਈ ਦੇ ਕੇਂਦਰ ਨੂੰ ਵਿਵਸਥਿਤ ਕਰੋ;
3. ਯੋਗ ਖਾਲੀ ਥਾਂਵਾਂ ਦੀ ਚੋਣ ਕਰੋ;
4. ਐਕਸਟਰਿਊਸ਼ਨ ਤਾਪਮਾਨ, ਐਕਸਟਰਿਊਸ਼ਨ ਸਪੀਡ ਅਤੇ ਹੋਰ ਪ੍ਰਕਿਰਿਆ ਪੈਰਾਮੀਟਰਾਂ ਦਾ ਵਾਜਬ ਨਿਯੰਤਰਣ।
XXV.(ਅਤੇ) ਮੂੰਹ ਫੈਲਾਓ
ਐਕਸਟਰੂਡ ਪ੍ਰੋਫਾਈਲ ਉਤਪਾਦਾਂ ਦੇ ਦੋਵੇਂ ਪਾਸੇ ਜਿਵੇਂ ਕਿ ਗਰੋਵ ਅਤੇ ਆਈ-ਆਕਾਰ ਵਾਲੇ ਨੁਕਸ ਨੂੰ ਫਲੇਅਰਿੰਗ ਕਿਹਾ ਜਾਂਦਾ ਹੈ, ਅਤੇ ਉਹ ਨੁਕਸ ਜੋ ਅੰਦਰ ਵੱਲ ਝੁਕਿਆ ਹੁੰਦਾ ਹੈ ਨੂੰ ਪੈਰਲਲ ਓਪਨਿੰਗ ਕਿਹਾ ਜਾਂਦਾ ਹੈ।
ਵਿਸਥਾਰ (ਇਕਸਾਰਤਾ) ਦੇ ਮੁੱਖ ਕਾਰਨ
1. ਦੋ "ਲੱਤਾਂ" (ਜਾਂ ਇੱਕ "ਲੱਤ") ਦੀ ਧਾਤੂ ਦੇ ਪ੍ਰਵਾਹ ਦੀ ਦਰ ਖੁਰਲੀ ਜਾਂ ਸਮਾਨ ਟਰੱਫ ਪ੍ਰੋਫਾਈਲਾਂ ਜਾਂ I-ਆਕਾਰ ਵਾਲੇ ਪ੍ਰੋਫਾਈਲਾਂ ਦੀ ਅਸਮਾਨ ਹੈ;
2. ਗਰੂਵ ਤਲ ਪਲੇਟ ਦੇ ਦੋਵੇਂ ਪਾਸੇ ਵਰਕਿੰਗ ਬੈਲਟ ਦੀ ਪ੍ਰਵਾਹ ਦਰ ਅਸਮਾਨ ਹੈ;
3. ਅਢੁਕਵੀਂ ਖਿੱਚਣ ਵਾਲੀ ਮਸ਼ੀਨ;
4. ਉਤਪਾਦ ਉੱਲੀ ਦੇ ਮੋਰੀ ਤੋਂ ਬਾਹਰ ਹੋਣ ਤੋਂ ਬਾਅਦ, ਔਨਲਾਈਨ ਹੱਲ ਇਲਾਜ ਅਸਮਾਨ ਤੌਰ 'ਤੇ ਠੰਢਾ ਹੁੰਦਾ ਹੈ.
ਰੋਕਥਾਮ ਵਿਧੀ
1. ਬਾਹਰ ਕੱਢਣ ਦੀ ਗਤੀ ਅਤੇ ਬਾਹਰ ਕੱਢਣ ਦੇ ਤਾਪਮਾਨ ਨੂੰ ਸਖਤੀ ਨਾਲ ਕੰਟਰੋਲ ਕਰੋ;
2. ਕੂਲਿੰਗ ਦੀ ਇਕਸਾਰਤਾ ਨੂੰ ਯਕੀਨੀ ਬਣਾਓ;
3. ਸਹੀ ਢੰਗ ਨਾਲ ਡਿਜ਼ਾਈਨ ਅਤੇ ਮੋਲਡ ਬਣਾਉਣਾ;
4. ਬਾਹਰ ਕੱਢਣ ਦੇ ਤਾਪਮਾਨ ਅਤੇ ਗਤੀ ਨੂੰ ਸਖਤੀ ਨਾਲ ਨਿਯੰਤਰਿਤ ਕਰੋ, ਅਤੇ ਟੂਲ ਨੂੰ ਸਥਾਪਿਤ ਕਰੋ ਅਤੇ ਸਹੀ ਢੰਗ ਨਾਲ ਮਰੋ।
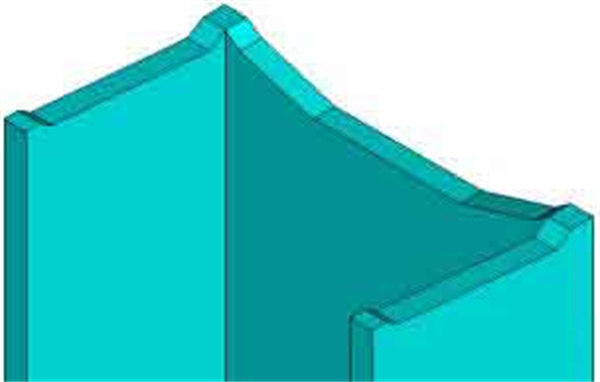
XXVI.ਸਿੱਧੇ ਕਰਨ ਦੇ ਨਿਸ਼ਾਨ
ਬਾਹਰ ਕੱਢੇ ਗਏ ਉਤਪਾਦ ਦੇ ਉੱਪਰਲੇ ਰੋਲ ਨੂੰ ਸਿੱਧੇ ਕੀਤੇ ਜਾਣ 'ਤੇ ਪੈਦਾ ਹੋਣ ਵਾਲੀਆਂ ਹੇਲੀਕਲ ਸਟ੍ਰੀਕਸ ਨੂੰ ਸਿੱਧੇ ਕਰਨ ਵਾਲੇ ਚਿੰਨ੍ਹ ਕਿਹਾ ਜਾਂਦਾ ਹੈ, ਅਤੇ ਉੱਪਰਲੇ ਰੋਲ ਦੁਆਰਾ ਸਿੱਧੇ ਕੀਤੇ ਗਏ ਕਿਸੇ ਵੀ ਉਤਪਾਦ ਲਈ ਸਿੱਧੇ ਕਰਨ ਵਾਲੇ ਚਿੰਨ੍ਹ ਤੋਂ ਬਚਿਆ ਨਹੀਂ ਜਾ ਸਕਦਾ।
ਨਿਸ਼ਾਨ ਸਿੱਧੇ ਹੋਣ ਦਾ ਮੁੱਖ ਕਾਰਨ
1. ਸਿੱਧਾ ਕਰਨ ਵਾਲੇ ਰੋਲਰ ਦੀ ਰੋਲਰ ਸਤਹ 'ਤੇ ਕਿਨਾਰੇ ਹਨ;
2. ਉਤਪਾਦ ਦਾ ਝੁਕਣਾ ਬਹੁਤ ਵੱਡਾ ਹੈ;
3. ਬਹੁਤ ਜ਼ਿਆਦਾ ਦਬਾਅ;
4. ਸਿੱਧਾ ਕਰਨ ਵਾਲੇ ਰੋਲਰ ਦਾ ਕੋਣ ਬਹੁਤ ਵੱਡਾ ਹੈ
5. ਉਤਪਾਦ ਦੀ ਇੱਕ ਵੱਡੀ ਅੰਡਾਕਾਰਤਾ ਹੈ.
ਰੋਕਥਾਮ ਵਿਧੀ
ਕਾਰਨ ਦੇ ਅਨੁਸਾਰ ਠੀਕ ਕਰਨ ਲਈ ਉਚਿਤ ਉਪਾਅ ਕਰੋ।
XXVII.ਰੁਕਣ ਦੇ ਨਿਸ਼ਾਨ, ਤਤਕਾਲ ਪ੍ਰਭਾਵ, ਦੰਦੀ ਦੇ ਨਿਸ਼ਾਨ
ਉਤਪਾਦ ਦੀ ਸਤ੍ਹਾ 'ਤੇ ਧਾਰੀਆਂ ਪੈਦਾ ਕਰਨ ਲਈ ਅਤੇ ਬਾਹਰ ਕੱਢਣ ਦੀ ਦਿਸ਼ਾ 'ਤੇ ਲੰਬਕਾਰੀ ਹੋਣ ਲਈ ਐਕਸਟਰਿਊਸ਼ਨ ਦੌਰਾਨ ਐਕਸਟਰਿਊਸ਼ਨ ਨੂੰ ਰੋਕੋ, ਜਿਸ ਨੂੰ ਸਟਾਪ ਮਾਰਕ ਕਹਿੰਦੇ ਹਨ;ਉਤਪਾਦ ਦੀ ਸਤ੍ਹਾ 'ਤੇ ਲਾਈਨ ਜਾਂ ਪੱਟੀਆਂ ਦੀਆਂ ਪੱਟੀਆਂ ਅਤੇ ਐਕਸਟਰਿਊਸ਼ਨ ਦੌਰਾਨ ਬਾਹਰ ਕੱਢਣ ਦੀ ਦਿਸ਼ਾ 'ਤੇ ਲੰਬਵਤ, ਜਿਸ ਨੂੰ ਦੰਦੀ ਦੇ ਨਿਸ਼ਾਨ ਜਾਂ ਤਤਕਾਲ ਛਾਪਾਂ ਵਜੋਂ ਜਾਣਿਆ ਜਾਂਦਾ ਹੈ (ਆਮ ਤੌਰ 'ਤੇ "ਜਾਅਲੀ ਪਾਰਕਿੰਗ ਚਿੰਨ੍ਹ" ਵਜੋਂ ਜਾਣਿਆ ਜਾਂਦਾ ਹੈ)
ਐਕਸਟਰਿਊਸ਼ਨ ਦੇ ਦੌਰਾਨ, ਅਟੈਚਮੈਂਟ ਜੋ ਕੰਮ ਕਰਨ ਵਾਲੀ ਪੱਟੀ ਦੀ ਸਤਹ 'ਤੇ ਸਥਿਰਤਾ ਨਾਲ ਚਿਪਕਦੇ ਹਨ, ਤੁਰੰਤ ਅਲੱਗ ਹੋ ਜਾਂਦੇ ਹਨ ਅਤੇ ਪੈਟਰਨ ਬਣਾਉਣ ਲਈ ਐਕਸਟਰੂਡ ਉਤਪਾਦ ਦੀ ਸਤਹ ਨਾਲ ਪਾਲਣਾ ਕਰਦੇ ਹਨ।ਵਰਕਿੰਗ ਬੈਲਟ ਦੀਆਂ ਖਿਤਿਜੀ ਧਾਰੀਆਂ ਜੋ ਬਾਹਰ ਨਿਕਲਣ ਦੇ ਬੰਦ ਹੋਣ 'ਤੇ ਦਿਖਾਈ ਦਿੰਦੀਆਂ ਹਨ, ਨੂੰ ਪਾਰਕਿੰਗ ਚਿੰਨ੍ਹ ਕਿਹਾ ਜਾਂਦਾ ਹੈ;ਬਾਹਰ ਕੱਢਣ ਦੀ ਪ੍ਰਕਿਰਿਆ ਦੌਰਾਨ ਦਿਖਾਈ ਦੇਣ ਵਾਲੀਆਂ ਧਾਰੀਆਂ ਨੂੰ ਤਤਕਾਲ ਪ੍ਰਭਾਵ ਜਾਂ ਦੰਦੀ ਦੇ ਨਿਸ਼ਾਨ ਕਿਹਾ ਜਾਂਦਾ ਹੈ, ਅਤੇ ਉਹ ਐਕਸਟਰਿਊਸ਼ਨ ਦੌਰਾਨ ਆਵਾਜ਼ ਬਣਾਉਣਗੀਆਂ।
ਰੁਕਣ ਦੇ ਨਿਸ਼ਾਨ, ਤੁਰੰਤ ਨਿਸ਼ਾਨ ਅਤੇ ਦੰਦੀ ਦੇ ਨਿਸ਼ਾਨ ਦੇ ਮੁੱਖ ਕਾਰਨ
1. ਇੰਗੋਟ ਦਾ ਅਸਮਾਨ ਹੀਟਿੰਗ ਤਾਪਮਾਨ ਜਾਂ ਐਕਸਟਰਿਊਸ਼ਨ ਸਪੀਡ ਅਤੇ ਦਬਾਅ ਵਿੱਚ ਅਚਾਨਕ ਤਬਦੀਲੀ;
2. ਉੱਲੀ ਦੇ ਮੁੱਖ ਹਿੱਸੇ ਮਾੜੇ ਢੰਗ ਨਾਲ ਤਿਆਰ ਕੀਤੇ ਗਏ ਹਨ ਅਤੇ ਨਿਰਮਿਤ ਹਨ, ਜਾਂ ਅਸੈਂਬਲੀ ਅਸਮਾਨ ਹੈ ਅਤੇ ਅੰਤਰ ਹਨ;
3. ਬਾਹਰ ਕੱਢਣ ਦੀ ਦਿਸ਼ਾ ਵਿੱਚ ਇੱਕ ਬਾਹਰੀ ਬਲ ਲੰਬਵਤ ਹੁੰਦਾ ਹੈ;
4. ਐਕਸਟਰੂਡਰ ਸੁਚਾਰੂ ਢੰਗ ਨਾਲ ਨਹੀਂ ਚੱਲਦਾ, ਅਤੇ ਰੇਂਗਣ ਦੀ ਇੱਕ ਘਟਨਾ ਹੈ.
ਰੋਕਥਾਮ ਵਿਧੀ
1. ਉੱਚ ਤਾਪਮਾਨ, ਹੌਲੀ ਗਤੀ ਅਤੇ ਇਕਸਾਰ ਐਕਸਟਰਿਊਸ਼ਨ, ਐਕਸਟਰਿਊਸ਼ਨ ਫੋਰਸ ਸਥਿਰ ਰਹਿੰਦੀ ਹੈ;
2. ਉਤਪਾਦ 'ਤੇ ਕੰਮ ਕਰਨ ਤੋਂ ਵਰਟੀਕਲ ਐਕਸਟਰਿਊਸ਼ਨ ਦਿਸ਼ਾ ਵਿੱਚ ਬਾਹਰੀ ਬਲ ਨੂੰ ਰੋਕੋ;
3. ਔਜ਼ਾਰਾਂ ਅਤੇ ਮੋਲਡਾਂ ਦਾ ਵਾਜਬ ਡਿਜ਼ਾਈਨ, ਉੱਲੀ ਸਮੱਗਰੀ ਦੀ ਸਹੀ ਚੋਣ, ਆਕਾਰ ਦਾ ਮੇਲ, ਤਾਕਤ ਅਤੇ ਕਠੋਰਤਾ।
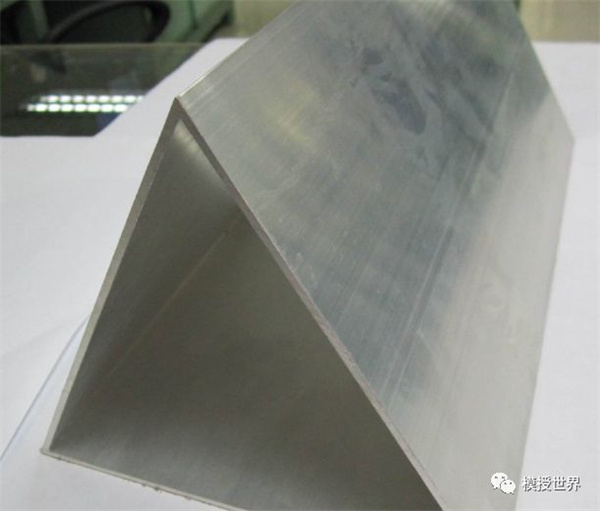
XXVIII.ਅੰਦਰਲੀ ਸਤ੍ਹਾ 'ਤੇ ਸਕ੍ਰੈਚ
ਬਾਹਰ ਕੱਢਣ ਦੀ ਪ੍ਰਕਿਰਿਆ ਦੌਰਾਨ ਬਾਹਰ ਕੱਢੇ ਗਏ ਉਤਪਾਦ ਦੀ ਅੰਦਰੂਨੀ ਸਤ੍ਹਾ 'ਤੇ ਖੁਰਚੀਆਂ ਨੂੰ ਅੰਦਰੂਨੀ ਸਤਹ ਦੇ ਖੁਰਚਿਆਂ ਕਿਹਾ ਜਾਂਦਾ ਹੈ।
ਅੰਦਰੂਨੀ ਸਤਹ ਦੇ ਘਬਰਾਹਟ ਦਾ ਮੁੱਖ ਕਾਰਨ
1. ਬਾਹਰ ਕੱਢਣ ਦੀ ਸੂਈ ਧਾਤ ਨਾਲ ਫਸ ਗਈ ਹੈ;
2. ਐਕਸਟਰਿਊਸ਼ਨ ਸੂਈ ਦਾ ਤਾਪਮਾਨ ਘੱਟ ਹੈ;
3. ਬਾਹਰ ਕੱਢਣ ਵਾਲੀ ਸੂਈ ਦੀ ਸਤਹ ਦੀ ਗੁਣਵੱਤਾ ਮਾੜੀ ਹੈ ਅਤੇ ਬੰਪਰ ਹਨ;
4. ਬਾਹਰ ਕੱਢਣ ਦਾ ਤਾਪਮਾਨ ਅਤੇ ਗਤੀ ਚੰਗੀ ਤਰ੍ਹਾਂ ਨਿਯੰਤਰਿਤ ਨਹੀਂ ਹੈ;
5. ਐਕਸਟਰਿਊਸ਼ਨ ਲੁਬਰੀਕੈਂਟ ਦਾ ਗਲਤ ਅਨੁਪਾਤ;
ਰੋਕਥਾਮ ਵਿਧੀ
1. ਐਕਸਟਰੂਜ਼ਨ ਸਿਲੰਡਰ ਅਤੇ ਐਕਸਟਰੂਜ਼ਨ ਸੂਈ ਦੇ ਤਾਪਮਾਨ ਨੂੰ ਵਧਾਓ, ਅਤੇ ਐਕਸਟਰੂਜ਼ਨ ਤਾਪਮਾਨ ਅਤੇ ਐਕਸਟਰੂਜ਼ਨ ਦੀ ਗਤੀ ਨੂੰ ਨਿਯੰਤਰਿਤ ਕਰੋ;
2. ਲੁਬਰੀਕੇਟਿੰਗ ਤੇਲ ਫਿਲਟਰੇਸ਼ਨ ਨੂੰ ਮਜ਼ਬੂਤ ਕਰੋ, ਕੂੜੇ ਦੇ ਤੇਲ ਦੀ ਜਾਂਚ ਕਰੋ ਜਾਂ ਬਦਲੋ, ਅਤੇ ਤੇਲ ਨੂੰ ਬਰਾਬਰ ਅਤੇ ਉਚਿਤ ਰੂਪ ਵਿੱਚ ਲਾਗੂ ਕਰੋ;
3. ਉੱਨ ਦੀ ਸਤ੍ਹਾ ਨੂੰ ਸਾਫ਼ ਰੱਖੋ;
4. ਅਯੋਗ ਮੋਲਡਾਂ ਅਤੇ ਐਕਸਟਰਿਊਸ਼ਨ ਸੂਈਆਂ ਨੂੰ ਸਮੇਂ ਸਿਰ ਬਦਲੋ, ਅਤੇ ਐਕਸਟਰਿਊਸ਼ਨ ਮੋਲਡਾਂ ਦੀ ਸਤਹ ਨੂੰ ਸਾਫ਼ ਅਤੇ ਨਿਰਵਿਘਨ ਰੱਖੋ।
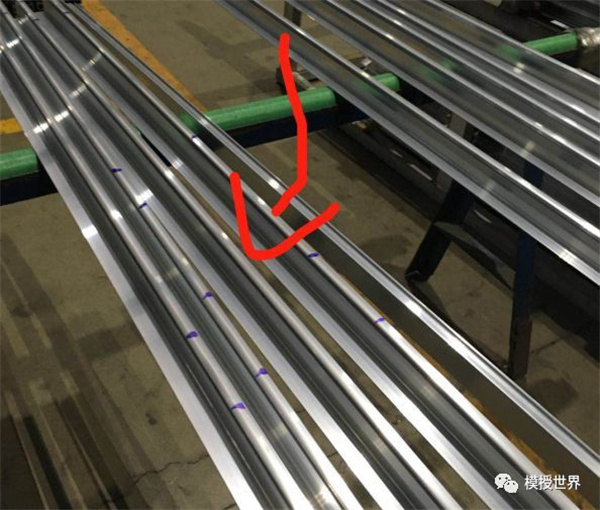
XXX.ਹੋਰ ਕਾਰਕ
ਇੱਕ ਸ਼ਬਦ ਵਿੱਚ, ਵਿਆਪਕ ਇਲਾਜ ਦੇ ਬਾਅਦ, ਉੱਪਰ ਦੱਸੇ ਗਏ ਅਲਮੀਨੀਅਮ ਮਿਸ਼ਰਤ ਐਕਸਟਰਿਊਸ਼ਨ ਉਤਪਾਦਾਂ ਦੇ 30 ਕਿਸਮਾਂ ਦੇ ਨੁਕਸ ਨੂੰ ਪ੍ਰਭਾਵਸ਼ਾਲੀ ਢੰਗ ਨਾਲ ਖਤਮ ਕੀਤਾ ਜਾ ਸਕਦਾ ਹੈ, ਉੱਚ ਗੁਣਵੱਤਾ, ਉੱਚ ਉਪਜ, ਲੰਬੀ ਉਮਰ, ਅਤੇ ਸੁੰਦਰ ਉਤਪਾਦ ਸਤਹ, ਇੱਕ ਬ੍ਰਾਂਡ ਬਣਾਉਣਾ, ਜੀਵਨਸ਼ਕਤੀ ਅਤੇ ਖੁਸ਼ਹਾਲੀ ਲਿਆਉਂਦਾ ਹੈ. ਉੱਦਮ, ਅਤੇ ਮਹੱਤਵਪੂਰਨ ਤਕਨੀਕੀ ਅਤੇ ਆਰਥਿਕ ਲਾਭ ਹੋਣ।
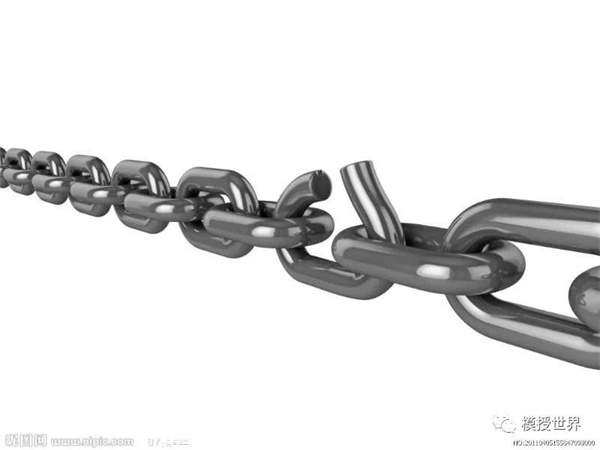
XXX.ਹੋਰ ਕਾਰਕ
ਇੱਕ ਸ਼ਬਦ ਵਿੱਚ, ਵਿਆਪਕ ਇਲਾਜ ਦੇ ਬਾਅਦ, ਉੱਪਰ ਦੱਸੇ ਗਏ ਅਲਮੀਨੀਅਮ ਮਿਸ਼ਰਤ ਐਕਸਟਰਿਊਸ਼ਨ ਉਤਪਾਦਾਂ ਦੇ 30 ਕਿਸਮਾਂ ਦੇ ਨੁਕਸ ਨੂੰ ਪ੍ਰਭਾਵਸ਼ਾਲੀ ਢੰਗ ਨਾਲ ਖਤਮ ਕੀਤਾ ਜਾ ਸਕਦਾ ਹੈ, ਉੱਚ ਗੁਣਵੱਤਾ, ਉੱਚ ਉਪਜ, ਲੰਬੀ ਉਮਰ, ਅਤੇ ਸੁੰਦਰ ਉਤਪਾਦ ਸਤਹ, ਇੱਕ ਬ੍ਰਾਂਡ ਬਣਾਉਣਾ, ਜੀਵਨਸ਼ਕਤੀ ਅਤੇ ਖੁਸ਼ਹਾਲੀ ਲਿਆਉਂਦਾ ਹੈ. ਉੱਦਮ, ਅਤੇ ਮਹੱਤਵਪੂਰਨ ਤਕਨੀਕੀ ਅਤੇ ਆਰਥਿਕ ਲਾਭ ਹੋਣ।
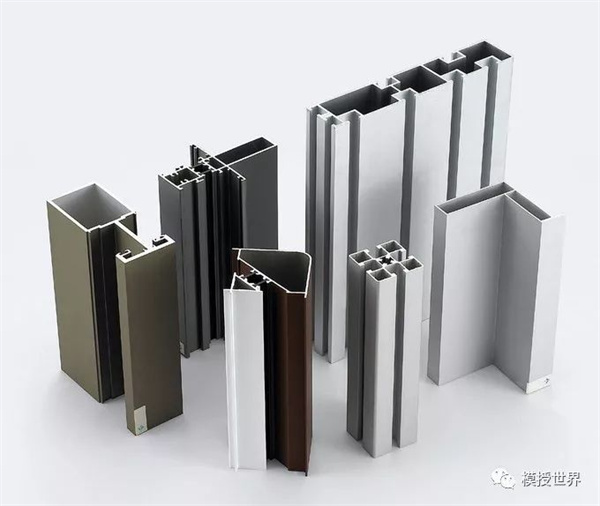
ਪੋਸਟ ਟਾਈਮ: ਅਗਸਤ-14-2022